Lost foam cast alloy steel coating and preparation method thereof
A technology of lost foam casting and alloy steel, applied in the field of coatings, which can solve the problems of poor adsorption and corrosion resistance, and achieve the effects of moderate coating temperature, high casting precision and low coating density
- Summary
- Abstract
- Description
- Claims
- Application Information
AI Technical Summary
Problems solved by technology
Method used
Examples
Embodiment 1
[0025] A lost foam casting alloy steel coating, the formula of which comprises the following components in parts by mass: 50 parts of zircon sand, 2 parts of bentonite, 2 parts of carboxymethyl cellulose, 1 part of Bailu gum, 3 parts of silica gel, and 2 parts of resin 3 parts of ethylene glycol, 1 part of attapulgite, 10 parts of n-butanol, 2 parts of casein, and 60 parts of water.
[0026] Among them, the specifications of zircon sand are as follows according to mass percentage: 4% below 100 mesh, 85% for 100-150 mesh, 7.5% for 150-200 mesh, and 0.6% for above 200 mesh.
[0027] In the present embodiment, the preparation method of the lost foam casting alloy steel coating comprises the following steps:
[0028] S1, put zircon sand, bentonite, and attapulgite into a mixing tank with a capacity of 800ml according to the ratio and stir evenly for 1 hour to obtain raw material A, which needs to be stored for 13 hours before use;
[0029] S2, put Bailu glue, silica gel and resin...
Embodiment 2
[0032] A lost foam casting alloy steel coating, the formula of which comprises the following components in parts by mass: 55 parts of zircon sand, 4 parts of bentonite, 3 parts of carboxymethyl cellulose, 2 parts of Bailu gum, 4 parts of silica gel, and 3 parts of resin 4 parts of ethylene glycol, 1.5 parts of attapulgite, 15 parts of n-butanol, 3 parts of casein, and 70 parts of water.
[0033] Among them, the specifications of zircon sand are as follows according to mass percentage: 4% below 100 mesh, 85% for 100-150 mesh, 7.5% for 150-200 mesh, and 0.6% for above 200 mesh.
[0034] In the present embodiment, the preparation method of the lost foam casting alloy steel coating comprises the following steps:
[0035] S1, put zircon sand, bentonite, and attapulgite into a mixing tank with a capacity of 900ml according to the ratio and stir evenly for 1.5 hours to obtain raw material A, which needs to be stored for 13 hours before use;
[0036] S2, put Bailu glue, silica gel an...
Embodiment 3
[0039] A lost foam casting alloy steel coating, the formula of which comprises the following components in parts by mass: 60 parts of zircon sand, 6 parts of bentonite, 4 parts of carboxymethyl cellulose, 3 parts of Bailu gum, 5 parts of silica gel, and 4 parts of resin 5 parts of ethylene glycol, 2 parts of attapulgite, 20 parts of n-butanol, 4 parts of casein, and 80 parts of water.
[0040] Among them, the specifications of zircon sand are as follows according to mass percentage: 4% below 100 mesh, 85% for 100-150 mesh, 7.5% for 150-200 mesh, and 0.6% for above 200 mesh.
[0041] In the present embodiment, the preparation method of the lost foam casting alloy steel coating comprises the following steps:
[0042] S1, put zircon sand, bentonite, and attapulgite into a mixing tank with a capacity of 1000ml according to the ratio and stir evenly for 2 hours to obtain raw material A, which needs to be stored for 13 hours before use;
[0043] S2, put Bailu glue, silica gel and r...
PUM
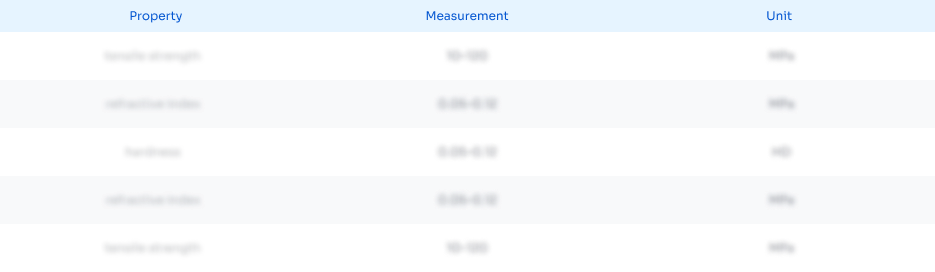
Abstract
Description
Claims
Application Information

- Generate Ideas
- Intellectual Property
- Life Sciences
- Materials
- Tech Scout
- Unparalleled Data Quality
- Higher Quality Content
- 60% Fewer Hallucinations
Browse by: Latest US Patents, China's latest patents, Technical Efficacy Thesaurus, Application Domain, Technology Topic, Popular Technical Reports.
© 2025 PatSnap. All rights reserved.Legal|Privacy policy|Modern Slavery Act Transparency Statement|Sitemap|About US| Contact US: help@patsnap.com