Skewering material cutting and skewering mold
A mold and trough technology, which is applied in the field of string cutting through molds, can solve the problems of low production efficiency and complicated operation, and achieve the effect of improving production efficiency and reducing the amount of preparation work.
- Summary
- Abstract
- Description
- Claims
- Application Information
AI Technical Summary
Problems solved by technology
Method used
Image
Examples
Embodiment 1
[0030] Such as Figure 1-3 As shown, the serial material in this embodiment cuts through the mold, including a first mold body 1 and a second mold body 2 that are fastened to each other.
[0031] On the first mold body 1, there are a plurality of first serial troughs 11 and first sign groove ribs 12 arranged in parallel at intervals along the transverse direction, and the first sign groove ribs 12 are longitudinally provided with first sign grooves 13; A mold body 1 is longitudinally spaced with a plurality of first feed grooves 14 arranged in parallel, and the first feed grooves 14 run through the rear end of the first mold body 1, the first stringing groove 11 and the first sign groove protrusion. Ridge 12, so that the first stringing chute 11 and the first signing groove rib 12 are separated, so that the first signing groove 13 and the first knife feeding groove 14 are arranged at intervals.
[0032] Correspondingly, on the second mold body 2, there are a plurality of para...
Embodiment 2
[0039] Such as Figure 4-6 As shown, the cross-cutting die of this embodiment has the same overall structure as that of the cross-cutting die in Embodiment 1. The difference between the two is:
[0040] In Embodiment 1, the first entry groove 14 and the second entry groove 24 do not pass through the front and rear ends of the first mold body 1 and the second mold body 2, and the first entry port 15 and the second entry port 25 are only arranged on the rear ends of the first mold body 1 and the second mold body 2 respectively, that is, the mold is only provided with the rear-end knife opening 3 and the rear-end entrance 4, and the cutter and the stick can only be drawn from one end of the mould. Enter.
[0041] In the second embodiment, the first infeed groove 14 and the second infeed groove 24 run through the front and rear ends of the first mold body 1 and the second mold body 2, respectively forming the front end knife edge 5 and the rear edge at the front and rear ends of th...
PUM
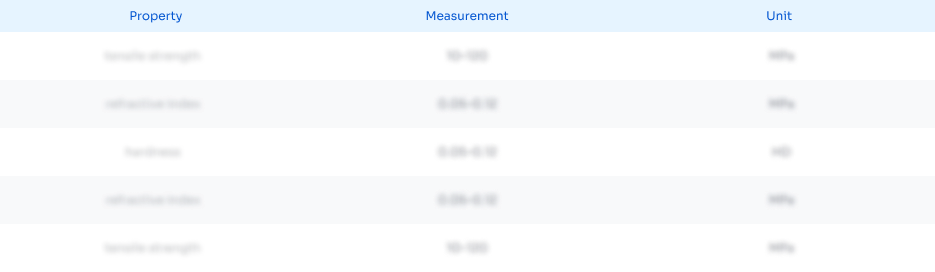
Abstract
Description
Claims
Application Information

- Generate Ideas
- Intellectual Property
- Life Sciences
- Materials
- Tech Scout
- Unparalleled Data Quality
- Higher Quality Content
- 60% Fewer Hallucinations
Browse by: Latest US Patents, China's latest patents, Technical Efficacy Thesaurus, Application Domain, Technology Topic, Popular Technical Reports.
© 2025 PatSnap. All rights reserved.Legal|Privacy policy|Modern Slavery Act Transparency Statement|Sitemap|About US| Contact US: help@patsnap.com