A kind of production method of chromate-free leather
A production method and chromic acid technology, which are applied in leather manufacturing, leather surface treatment, small raw hide/large raw hide/leather/fur treatment, etc., can solve the problem of increased pressure difference in the cortex, formation of gray spots, and long lime leaching time. and other problems, to achieve the effect of reducing sodium hydroxide, softening the skin and reducing swelling of the skin
- Summary
- Abstract
- Description
- Claims
- Application Information
AI Technical Summary
Problems solved by technology
Method used
Examples
Embodiment 1
[0023] This embodiment provides a method for making chromium-free pickled leather. The following steps are carried out in sequence: fur immersion → flesh removal → pre-degreasing → enzyme depilation → soaking in alkali → sliced skin → dealkalization → degreasing and softening → pickling → pickling, with Take yellow leather as an example.
[0024] Wherein: immersion and de-fleshing can be done by conventional techniques, and the specific operation process of the pre-degreasing process is: the de-fleshed skin is placed in the drum, the control liquid ratio is 1.0, and 0.2% (owf) of Pastosol U and 1.0% (owf) Alkaline degreasing enzyme Greasex 50L, after drumming for 40min, perform enzymatic hair removal directly.
[0025] The specific operation process of the enzyme depilation process is: continue to add 0.4% (owf) 166 neutral protease, 0.2% (owf) trypsin and 0.5% (owf) glutamine to the drum after the pre-degreasing is completed Sodium acid, the liquid temperature is 36 ℃ ~ 40...
Embodiment 2
[0031] This embodiment provides a method for making chromium-free pickled leather. The following steps are carried out in sequence: fur immersion → flesh removal → pre-degreasing → enzyme depilation → soaking in alkali → sliced skin → dealkalization → degreasing and softening → pickling → pickling, with Take yellow leather as an example.
[0032] Wherein: immersion and de-fleshing can be done by conventional techniques, and the specific operation process of the pre-degreasing process is: the de-fleshed skin is placed in the drum, the control liquid ratio is 1.5, and 0.4% (owf) Pastosol U and 1.0% (owf) Alkaline degreasing enzyme Greasex 50L, after drumming for 35min, perform enzymatic hair removal directly.
[0033] The specific operation process of the enzyme depilation process is: continue to add 0.5% (owf) of AS1.398 neutral protease, 0.3% (owf) of trypsin and 0.6% (owf) of Sodium glutamate, the liquid temperature is 36 ℃ ~ 40 ℃, stop the drum for 30 minutes after every 30...
Embodiment 3
[0039] This embodiment provides a method for making chromium-free pickled leather. The following steps are carried out in sequence: fur immersion → flesh removal → pre-degreasing → enzyme depilation → soaking in alkali → sliced skin → dealkalization → degreasing and softening → pickling → pickling, with Take yellow leather as an example.
[0040] Wherein: immersion and de-fleshing can be done by conventional techniques, and the specific operation process of the pre-degreasing process is: the de-fleshed skin is placed in the drum, the control liquid ratio is 1.2, and 0.3% (owf) of Pastosol U and 1.2% are added. (owf) alkaline degreasing enzyme Greasex 50L, after drumming for 30min, perform enzymatic hair removal directly.
[0041] The specific operation process of the enzyme depilation process is: continue to add 0.3% (owf)-166 neutral protease, 0.2% (owf) AS1.398 neutral enzyme, 0.2% (owf) to the drum after the pre-degreasing is completed. ) trypsin and 0.8% (owf) sodium gl...
PUM
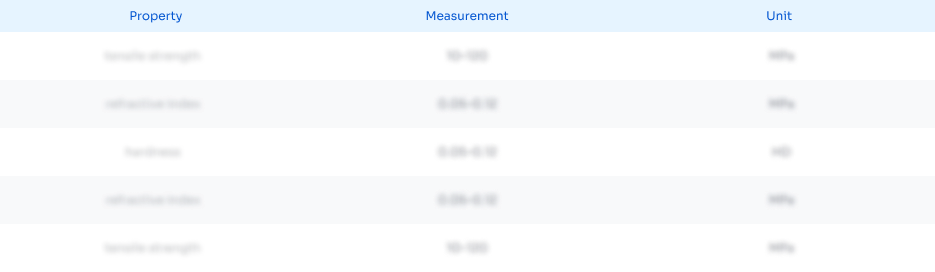
Abstract
Description
Claims
Application Information

- R&D
- Intellectual Property
- Life Sciences
- Materials
- Tech Scout
- Unparalleled Data Quality
- Higher Quality Content
- 60% Fewer Hallucinations
Browse by: Latest US Patents, China's latest patents, Technical Efficacy Thesaurus, Application Domain, Technology Topic, Popular Technical Reports.
© 2025 PatSnap. All rights reserved.Legal|Privacy policy|Modern Slavery Act Transparency Statement|Sitemap|About US| Contact US: help@patsnap.com