A kind of separation and recycling granulator of waste plastic output by screwing
A technology for separating and recycling waste plastics, applied in the field of separation and recycling granulators, can solve the problems of reducing the surface flatness of plastic pellets, reducing the production efficiency of plastic pellets, and insufficient technical considerations, so as to improve quality, improve production efficiency, and avoid problems. ripped off effect
- Summary
- Abstract
- Description
- Claims
- Application Information
AI Technical Summary
Problems solved by technology
Method used
Image
Examples
Embodiment
[0028] see Figure 1-Figure 2 , the present invention provides a separation and recovery granulator for waste plastics output by screwing, its structure includes a plastic feed hopper 1, a granulation extrusion device 2, an equipment support frame 3, a drive motor 4, and a drive coupling 5 , the equipment support frame 3 is a hollow rectangular structure and the bottom surface is close to the workshop floor, the bottom surface of the granulation extrusion device 2 and the upper surface of the equipment support frame 3 are fixed together by bolts, and the drive motor 4 is located at the On the right side of the upper surface of the granulation extrusion device 2, the left and right ends of the drive coupling 5 are engaged with the granulation extrusion device 2 and the drive motor 4 respectively, and the bottom of the plastic feeding hopper 1 is connected to the granulation extrusion device 2 are connected to each other and are perpendicular to each other. The granulation extru...
PUM
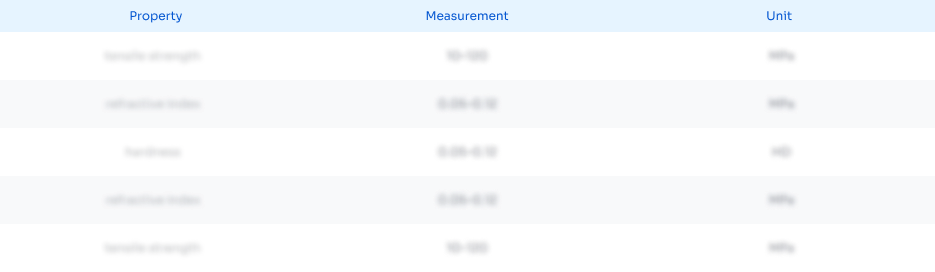
Abstract
Description
Claims
Application Information

- R&D Engineer
- R&D Manager
- IP Professional
- Industry Leading Data Capabilities
- Powerful AI technology
- Patent DNA Extraction
Browse by: Latest US Patents, China's latest patents, Technical Efficacy Thesaurus, Application Domain, Technology Topic, Popular Technical Reports.
© 2024 PatSnap. All rights reserved.Legal|Privacy policy|Modern Slavery Act Transparency Statement|Sitemap|About US| Contact US: help@patsnap.com