Flue gas guiding system and method as well as waste heat boiler
A waste heat boiler and flue gas flow rate technology, which is applied in the field of waste heat boilers and gas turbine waste heat boilers, can solve the problems of increased heat dissipation loss of boilers, increased equipment manufacturing costs, and large impact of guide plates, so as to reduce flue gas resistance and ensure Effective utilization, uniform flow effect
- Summary
- Abstract
- Description
- Claims
- Application Information
AI Technical Summary
Problems solved by technology
Method used
Image
Examples
Embodiment Construction
[0066] The details of the present invention can be understood more clearly with reference to the accompanying drawings and the description of specific embodiments of the present invention. However, the specific embodiments of the present invention described here are only for the purpose of explaining the present invention, and should not be construed as limiting the present invention in any way. Under the teaching of the present invention, the skilled person can conceive any possible modification based on the present invention, and these should be regarded as belonging to the scope of the present invention.
[0067] Such as Figure 1 to Figure 8 As shown, the flue gas guiding system 10 proposed by the present invention includes a plurality of guiding devices 11, a plurality of flue gas velocity detection devices and a control unit (not shown in the figure), wherein the plurality of guiding devices 11 are used for guiding waste heat For flue gas in the inlet flue 20 of the boi...
PUM
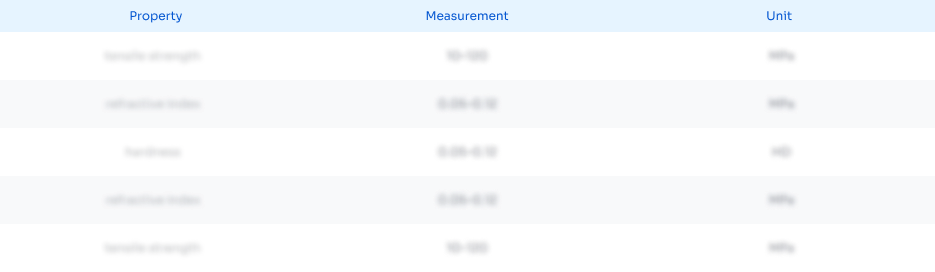
Abstract
Description
Claims
Application Information

- R&D
- Intellectual Property
- Life Sciences
- Materials
- Tech Scout
- Unparalleled Data Quality
- Higher Quality Content
- 60% Fewer Hallucinations
Browse by: Latest US Patents, China's latest patents, Technical Efficacy Thesaurus, Application Domain, Technology Topic, Popular Technical Reports.
© 2025 PatSnap. All rights reserved.Legal|Privacy policy|Modern Slavery Act Transparency Statement|Sitemap|About US| Contact US: help@patsnap.com