Robot laser cleaning path planning system and method based on computer vision
A technology of laser cleaning and path planning, which is applied to chemical instruments and methods, cleaning methods and tools, manipulators, etc., to achieve broad application prospects and improve work efficiency
- Summary
- Abstract
- Description
- Claims
- Application Information
AI Technical Summary
Problems solved by technology
Method used
Image
Examples
Embodiment Construction
[0028] In order to have a clearer understanding of the technical features, purposes and effects of the present invention, the specific implementation manners of the present invention will now be described in detail with reference to the accompanying drawings.
[0029] Please refer to figure 1 , which is a structural diagram of the manipulator teaching system in the present invention. In a manipulator teaching system proposed in the present invention, the system includes a visual motion capture module, a computer workstation, a teaching device and a manipulator, wherein:
[0030] 1. Visual capture module:
[0031] The visual motion capture module includes 8 infrared cameras, and each camera is fixed by a pan-tilt bracket, and the distance of each camera from the ground is 2.5 meters; Arranged in the field in a square shape, the radius of the square is 3 meters long, and the center of each infrared camera is aligned with the operating area of the workpiece table; on the other...
PUM
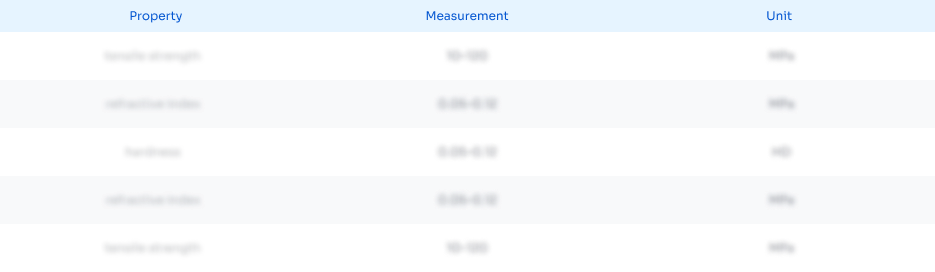
Abstract
Description
Claims
Application Information

- R&D
- Intellectual Property
- Life Sciences
- Materials
- Tech Scout
- Unparalleled Data Quality
- Higher Quality Content
- 60% Fewer Hallucinations
Browse by: Latest US Patents, China's latest patents, Technical Efficacy Thesaurus, Application Domain, Technology Topic, Popular Technical Reports.
© 2025 PatSnap. All rights reserved.Legal|Privacy policy|Modern Slavery Act Transparency Statement|Sitemap|About US| Contact US: help@patsnap.com