Online self-calibration system for micro-silicon mechanical gyroscope scale factor
A silicon micromachine and scale factor technology, applied in instruments, measuring devices, etc., can solve the problems of inability to apply the service life of silicon micromachine gyroscopes, difficult to achieve error compensation, complicated coupling mechanism, etc., to reduce volume and cost. , the effect of reducing power consumption, reducing design difficulty and processing difficulty
- Summary
- Abstract
- Description
- Claims
- Application Information
AI Technical Summary
Problems solved by technology
Method used
Image
Examples
Embodiment Construction
[0018] The present invention will be further introduced below in conjunction with the accompanying drawings and specific embodiments.
[0019] combine figure 1 , a kind of silicon micromechanical gyroscope scale factor on-line self-calibration system of the present invention, comprises C / V drive detection interface circuit, C / V detection interface circuit, automatic gain control circuit AGC, control switch, field programmable gate array FPGA , digital-to-analog converter DAC, analog-to-digital converter ADC;
[0020] The input terminal of the gyroscope C / V drive detection interface circuit is connected to the drive detection electrode of the silicon micromechanical gyroscope, and the drive detection current signal Ids obtained by driving the detection electrode is converted into a drive detection voltage Vds signal; the automatic gain control circuit AGC Controlling the amplitude of the driving detection voltage Vds signal, outputting the driving voltage Vd to the driving ele...
PUM
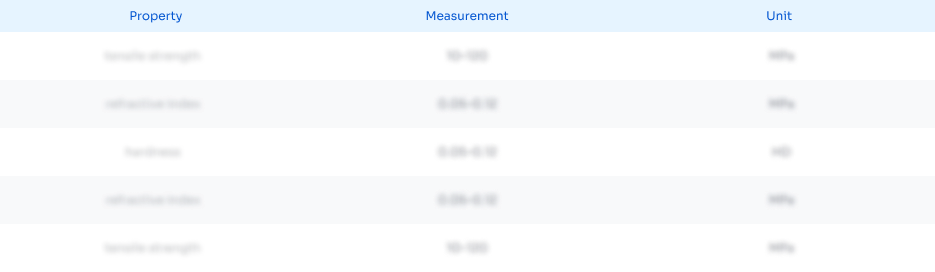
Abstract
Description
Claims
Application Information

- R&D Engineer
- R&D Manager
- IP Professional
- Industry Leading Data Capabilities
- Powerful AI technology
- Patent DNA Extraction
Browse by: Latest US Patents, China's latest patents, Technical Efficacy Thesaurus, Application Domain, Technology Topic, Popular Technical Reports.
© 2024 PatSnap. All rights reserved.Legal|Privacy policy|Modern Slavery Act Transparency Statement|Sitemap|About US| Contact US: help@patsnap.com