Preparation technology of glass fiber F9 grade air filtering material
A technology of air filter material and glass fiber, which is applied in the field of air filter material preparation, can solve the problems of thicker fiber diameter, reduced service life, and filter material failure, and achieves the advantages of easy back-blowing cleaning, obvious increase in resistance, and extended service life Effect
- Summary
- Abstract
- Description
- Claims
- Application Information
AI Technical Summary
Problems solved by technology
Method used
Examples
Embodiment 1
[0023] In the embodiment of the present invention, a kind of preparation technology of glass fiber F9 grade air filter material, take raw material by weight: 30% of the glass fiber of 10-12um, 55% of the glass fiber of 5-8um and 15% of glass wool, in raw material Add 20 times of raw material weight pH value to the water of 2.6, mix, stir into slurry, and ensure that the pH value of slurry is 2.5; Slurry is made filter material by existing wet papermaking molding method; Filter material with The paper feeding speed of 35m / min passes through three groups of drying cylinders successively, and the steam temperature in the three groups of drying cylinders is 90°C-110°C, 115°C-125°C, 125°C-145°C in order to dry the filter material, so that The water content of the dried filter material is less than 5%; the acrylic resin liquid (composed of 1 part of acrylic resin and 2 parts of water by weight) is coated on both sides of the dried filter material, and then the paper is fed at a speed...
Embodiment 2
[0025] Raw materials by weight ratio: 35% of 10-12um glass fiber, 53% of 5-8um glass fiber and 12% of glass wool, add 30 times the weight of raw material to the raw material, and add water with a pH value of 3.2, mix and stir to form a slurry , and ensure that the pH value of the slurry is 3.0; the slurry is made into a filter material according to the existing wet papermaking method; the filter material is passed through three groups of drying cylinders at a paper feeding speed of 45m / min, and the three groups of drying cylinders The steam temperature is 90°C-110°C, 115°C-125°C, 125°C-145°C in order to dry the filter material so that the water content of the dried filter material is less than 5%; the acrylic resin liquid (by weight) Composed of 1 part of acrylic resin and 2 parts of water) coated on both sides of the dried filter material, and then passed through two groups of drying cylinders at a speed of 45m / min, the steam temperature in the two groups of drying cylinders i...
Embodiment 3
[0027] Raw materials by weight ratio: 32% of 10-12um glass fiber, 50% of 5-8um glass fiber and 18% of glass wool, add 25 times the weight of raw material to the raw material with a pH value of 3.0, mix and stir to form a slurry , and ensure that the pH value of the slurry is 2.8; the slurry is made into a filter material according to the existing wet papermaking method; the filter material is passed through three groups of drying cylinders at a paper feeding speed of 40m / min, and the three groups of drying cylinders The steam temperature is 90°C-110°C, 115°C-125°C, 125°C-145°C in order to dry the filter material so that the water content of the dried filter material is less than 5%; Consists of 1 part of acrylic resin and 2 parts of water) coated on both sides of the dried filter material, and then passed through two groups of drying cylinders at a speed of 40m / min. The steam temperature in the two groups of drying cylinders is 90°C- 110°C, 120°C-140°C, to dry the filter mater...
PUM
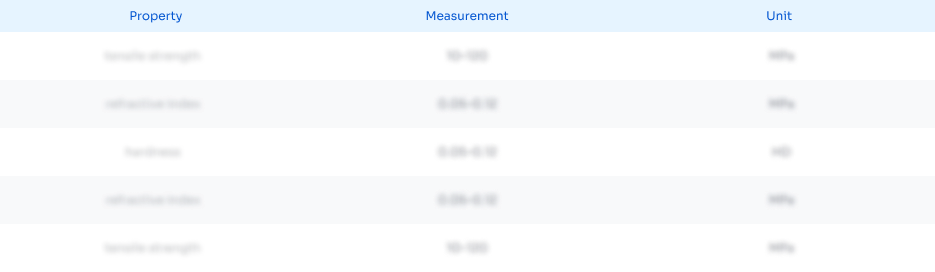
Abstract
Description
Claims
Application Information

- R&D
- Intellectual Property
- Life Sciences
- Materials
- Tech Scout
- Unparalleled Data Quality
- Higher Quality Content
- 60% Fewer Hallucinations
Browse by: Latest US Patents, China's latest patents, Technical Efficacy Thesaurus, Application Domain, Technology Topic, Popular Technical Reports.
© 2025 PatSnap. All rights reserved.Legal|Privacy policy|Modern Slavery Act Transparency Statement|Sitemap|About US| Contact US: help@patsnap.com