High-magnetic permeability composite material powder and preparation method thereof
A technology of composite materials and high magnetic permeability, which is applied in the direction of magnetic materials, magnetic core manufacturing, inductor/transformer/magnet manufacturing, etc., can solve the problems of high magnetic permeability and poor characteristics, and achieve high tap density, high stacking, Effect of Good DC Superposition Characteristics
- Summary
- Abstract
- Description
- Claims
- Application Information
AI Technical Summary
Problems solved by technology
Method used
Image
Examples
Embodiment 1
[0035] The preparation method of a kind of high magnetic permeability composite material powder of the present embodiment specifically comprises the following steps:
[0036](1) Ingredients: sieve the vacuum air-atomized FeSiAl with a rotary vibrating sieve, take -250 mesh powder, and sieve the gas-atomized iron-silicon material with a rotary vibrating sieve, take -400 mesh powder, Vacuum air-atomized iron-nickel is sieved with a rotary vibrating sieve, and the +400 mesh powder is taken, and mixed according to 1.8:0.8:3, and the specific vacuum air-atomized iron-silicon-alumina powder below -250 mesh: 18 kg;- Aerosolized iron-silicon powder below 400 mesh: 8 kg; Vacuum air-atomized iron-nickel powder above 400 mesh: 30 kg, using a V-type mixer for 30 minutes;
[0037] (2) Insulation coating: In a vertical mixer, put the mixed powder into a stirring pot heated to 90°C. When the powder temperature reaches 50°C, add 0.3% liquid silicone resin with a solid content of 15%. The wei...
Embodiment 2
[0061] The preparation method of a kind of high magnetic permeability composite material powder of the present embodiment specifically comprises the following steps:
[0062] (1) Ingredients: sieve the vacuum air-atomized iron-silicon-alumina with a rotary vibrating sieve, take -250 mesh powder, and sieve the gas-atomized iron-silicon material with a rotary vibrating sieve, take -400 mesh powder, Vacuum air-atomized iron-nickel is sieved with a rotary vibrating sieve, and the +400 mesh powder is taken, and mixed according to 2.2:1.2:3.4. The specific vacuum air-atomized iron-silicon-aluminum powder below -250 mesh: 22 kg;- Gas-atomized iron-silicon powder below 400 mesh: 12 kg; vacuum-atomized iron-nickel powder above 400 mesh: 34 kg, using a V-type mixer for 50 minutes;
[0063] (2) Insulation coating: Put the mixed powder into a stirring pot heated to 80°C. When the powder temperature reaches 60°C, add 1.0% liquid silicone resin with a solid content of 15%. The specific weig...
Embodiment 3
[0087] The preparation method of a kind of high magnetic permeability composite material powder of the present embodiment specifically comprises the following steps:
[0088] (1) Ingredients: sieve the vacuum air-atomized FeSiAl with a rotary vibrating sieve, take -250 mesh powder, and sieve the gas-atomized iron-silicon material with a rotary vibrating sieve, take -400 mesh powder, Vacuum air-atomized iron-nickel is sieved with a rotary vibrating sieve, and the +400 mesh powder is taken, and mixed according to 2.2:1:3. The specific vacuum air-atomized iron-silicon-alumina powder below -250 mesh: 22 kg;- Aerosolized iron-silicon powder below 400 mesh: 10 kg; vacuum air-atomized iron-nickel powder above 400 mesh: 30 kg, using a V-type mixer for 30 minutes;
[0089](2) Insulation coating: Put the mixed powder into a stirring pot heated to 100°C. When the temperature of the powder reaches 45°C, add 1.0% liquid silicone resin with a solid content of 15%. The specific weight of the...
PUM
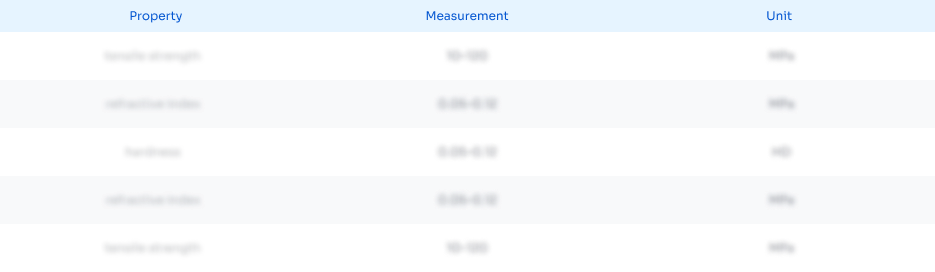
Abstract
Description
Claims
Application Information

- Generate Ideas
- Intellectual Property
- Life Sciences
- Materials
- Tech Scout
- Unparalleled Data Quality
- Higher Quality Content
- 60% Fewer Hallucinations
Browse by: Latest US Patents, China's latest patents, Technical Efficacy Thesaurus, Application Domain, Technology Topic, Popular Technical Reports.
© 2025 PatSnap. All rights reserved.Legal|Privacy policy|Modern Slavery Act Transparency Statement|Sitemap|About US| Contact US: help@patsnap.com