Full-closed-loop nonlinear prediction control method and system for servo press
A servo press and non-linear prediction technology, applied in the direction of presses, manufacturing tools, etc., can solve problems affecting repeat positioning accuracy, position control accuracy, and system errors, so as to improve production and processing technology, reduce workload, and improve mold quality. The effect of longevity
- Summary
- Abstract
- Description
- Claims
- Application Information
AI Technical Summary
Problems solved by technology
Method used
Image
Examples
Embodiment Construction
[0032] Accompanying drawing is a kind of specific embodiment of the present invention. In this embodiment, a servo press connected to a servo motor 2 is provided with a controller 1 and a slider 3 located on a working platform 4. The controller 1 controls and connects the servo motor 2 through a servo motor algorithm, and the servo motor 2 passes The transmission system 6 pulls the slider 3, and a grating ruler displacement sensor 5 is installed on the working platform 4 where the slider 3 is located. The grating ruler displacement sensor 5 is connected to the controller 1, and the servo motor 2 is connected to the controller 1 through the motor sensor 7. The motor sensor 7 connected to the servo motor 2 is provided with a position detection unit, a speed detection unit and a torque detection unit; the servo motor 2 is a permanent magnet synchronous motor.
[0033] The invention provides a full-closed-loop control method that can directly control the position of the slider, in...
PUM
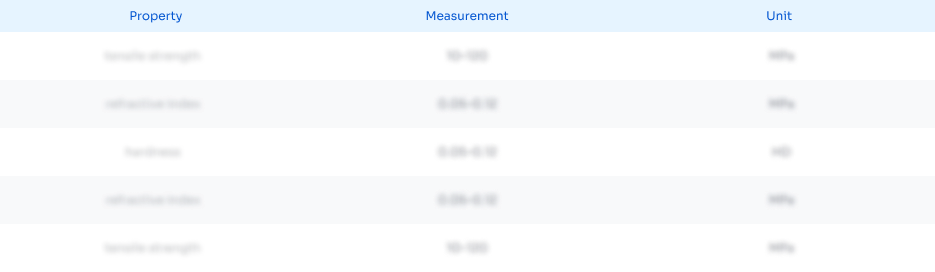
Abstract
Description
Claims
Application Information

- R&D Engineer
- R&D Manager
- IP Professional
- Industry Leading Data Capabilities
- Powerful AI technology
- Patent DNA Extraction
Browse by: Latest US Patents, China's latest patents, Technical Efficacy Thesaurus, Application Domain, Technology Topic, Popular Technical Reports.
© 2024 PatSnap. All rights reserved.Legal|Privacy policy|Modern Slavery Act Transparency Statement|Sitemap|About US| Contact US: help@patsnap.com