Electromechanical impedance monitoring method of bolt pre-tightening force under vibration excitation
A technology of bolt pre-tightening force and electromechanical impedance, applied in the measurement of resistance/reactance/impedance, testing of mechanical parts, testing of machine/structural parts, etc., can solve the problem of insufficient sensitivity and achieve the effect of improving sensitivity
- Summary
- Abstract
- Description
- Claims
- Application Information
AI Technical Summary
Problems solved by technology
Method used
Image
Examples
Embodiment Construction
[0024] Now in conjunction with embodiment, accompanying drawing, the present invention will be further described:
[0025] Concrete steps of the present invention are as follows:
[0026] Step 1: Paste the piezoelectric ceramic PZT on one side of the bolt to be tested, the main deformation direction of the bolt and the PZT sheet is in line, and connect the lead-out line of the piezoelectric sheet to the impedance analyzer;
[0027] Step 2: Fix the vibrator under the structure to be tested and connect it with the signal amplifier and signal generator;
[0028] Step 3: The sweep frequency range of the impedance analyzer can be set to 30-500kHz. At the same time, the signal generator sends out a sinusoidal pulse signal with a fixed frequency (200-1000Hz is enough) as the input signal of the exciter. Change the pre-tightening force of the bolts so that it gradually changes from completely loose to fully tightened (the specific value depends on the bolt used). After changing the ...
PUM
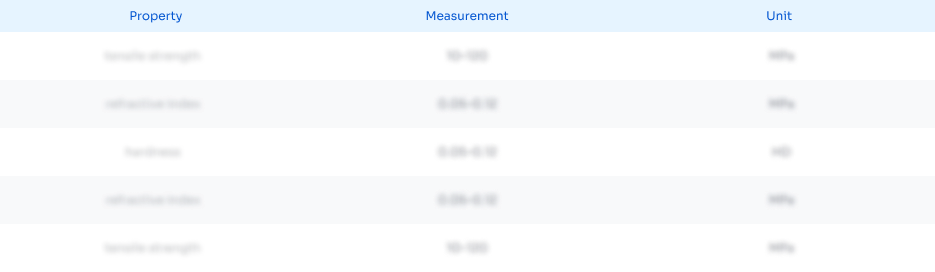
Abstract
Description
Claims
Application Information

- R&D Engineer
- R&D Manager
- IP Professional
- Industry Leading Data Capabilities
- Powerful AI technology
- Patent DNA Extraction
Browse by: Latest US Patents, China's latest patents, Technical Efficacy Thesaurus, Application Domain, Technology Topic, Popular Technical Reports.
© 2024 PatSnap. All rights reserved.Legal|Privacy policy|Modern Slavery Act Transparency Statement|Sitemap|About US| Contact US: help@patsnap.com