Secondary bioleaching continuous process for efficiently removing heavy metal chromium from leather making sludge
A technology of tannery sludge and biological leaching, which is applied in the direction of water pollutants, biological sludge treatment, animal processing wastewater treatment, etc., and can solve the problems of low sludge treatment efficiency, long leaching cycle, and different habitats provided by different microorganisms, etc. question
- Summary
- Abstract
- Description
- Claims
- Application Information
AI Technical Summary
Problems solved by technology
Method used
Image
Examples
Embodiment 1
[0028] This example provides a method for continuous and repeated batch bioleaching of tannery sludge in a mechanically stirred single-stage reactor, and the specific operations are as follows:
[0029] 1. The influence of feed ratio FR on single-stage reactor A:
[0030] (1) Processing method:
[0031] Using Community-S as the inoculum, bioleaching experiments under different feed ratios (FR) were carried out in a continuous mechanically stirred single-stage reactor A. The height / diameter ratio of the bioleaching reactor is 1.22; the amount of sulfur powder added is 0.5% (w / v) when the reactor is started, the inoculation amount of the enriched colony is 10% (v / v), and the concentration of tannery sludge is 2 % (w / v), made up to a working volume of 2700 mL with ultrapure water.
[0032] Under the condition of sludge concentration TS of 2%, bioleaching experiments with FR of 0.1 and 0.2 were carried out to study the relationship between FR and sludge treatment rate and leachi...
Embodiment 2
[0043] This embodiment provides a method for continuous and repeated batch bioleaching of tannery sludge in a mechanically stirred secondary reactor, and the specific operations are as follows:
[0044] (1) Processing method:
[0045] Bioleaching experiments under different FR and different TS conditions were carried out in a continuous mechanically stirred secondary reactor C using Community-S as the inoculum. The secondary reactor is composed of two single-stage reactors connected in series, and each single-stage reactor has the same structure as the single-stage reactor A. The first stage of the reactor provides biological pre-acidification function, and the reaction working volume of this stage is 1000mL, named Stage 1. The second stage is the main body of the bioleaching reactor, with a working volume of 2700mL, named Stage 2. The start-up conditions of Stage 1 and Stage 2 of this reactor are consistent with those of a single-stage reactor.
[0046] It works like figu...
PUM
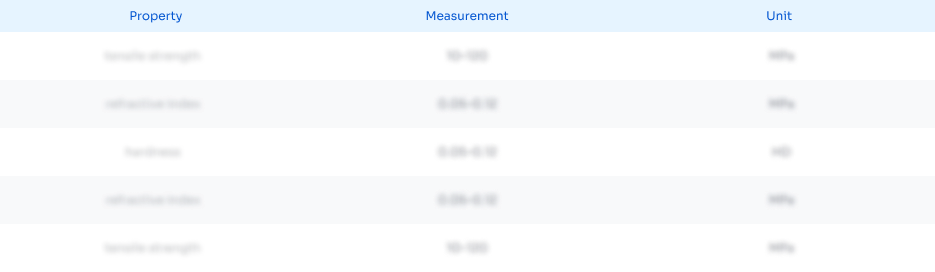
Abstract
Description
Claims
Application Information

- R&D
- Intellectual Property
- Life Sciences
- Materials
- Tech Scout
- Unparalleled Data Quality
- Higher Quality Content
- 60% Fewer Hallucinations
Browse by: Latest US Patents, China's latest patents, Technical Efficacy Thesaurus, Application Domain, Technology Topic, Popular Technical Reports.
© 2025 PatSnap. All rights reserved.Legal|Privacy policy|Modern Slavery Act Transparency Statement|Sitemap|About US| Contact US: help@patsnap.com