Industrial robot visual servo system and servo method and device
An industrial robot and visual servo technology, applied in the field of robotics, can solve the problems of high manpower cost, increased difficulty of visual recognition, prone to omissions and errors, etc., to facilitate operation and management, realize real-time tracking, and improve workflow Effect
- Summary
- Abstract
- Description
- Claims
- Application Information
AI Technical Summary
Problems solved by technology
Method used
Image
Examples
Embodiment Construction
[0050] The specific embodiments of the present invention will be further described below in conjunction with the accompanying drawings. The following examples are only used to illustrate the technical solution of the present invention more clearly, but not to limit the protection scope of the present invention.
[0051] figure 1 It shows a schematic diagram of the composition of an industrial robot visual servo system provided in this embodiment, including: a six-axis robot 201, a seam tracker 202, a calibration object 203, a wireless handheld teaching device 204, a USB wireless receiver 205, an infrared Laser positioning base station 206, robot control cabinet 207, welding machine power supply control cabinet 208, upper computer control cabinet 209 and automatic wire feeding system.
[0052] The seam tracker 202 is fixed on the first end of the six-axis robot 201 and connected to the upper computer control cabinet 209 through Ethernet.
[0053] The calibration object 203 is...
PUM
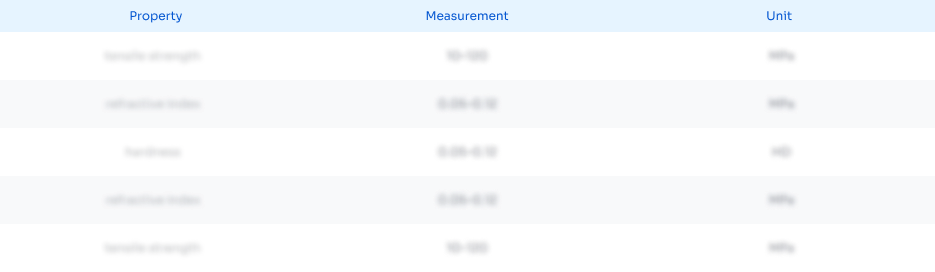
Abstract
Description
Claims
Application Information

- R&D Engineer
- R&D Manager
- IP Professional
- Industry Leading Data Capabilities
- Powerful AI technology
- Patent DNA Extraction
Browse by: Latest US Patents, China's latest patents, Technical Efficacy Thesaurus, Application Domain, Technology Topic, Popular Technical Reports.
© 2024 PatSnap. All rights reserved.Legal|Privacy policy|Modern Slavery Act Transparency Statement|Sitemap|About US| Contact US: help@patsnap.com