Torque pulsation restraining method of low-speed direct-drive permanent magnet motor servo system
A permanent magnet motor and servo system technology, which is applied in the fields of torque ripple suppression and speed crawling, and can solve the problems of no-load potential, power output capability, increased manufacturing cost, weakening of cogging torque amplitude, motor jitter and crawling, etc. , to achieve the effect of eliminating electromagnetic brakes, suppressing torque ripple, and eliminating compensation lag
- Summary
- Abstract
- Description
- Claims
- Application Information
AI Technical Summary
Problems solved by technology
Method used
Image
Examples
Embodiment Construction
[0026] The technical solution of the invention will be described in detail below in conjunction with the accompanying drawings.
[0027] The cogging torque is uneven in magnitude and distributed in positive and negative directions within one circle of the motor circumference. This positive and negative distributed force enables the motor to be positioned at a certain position. The positioning effect produced by it is as follows: figure 1 As shown, when the cogging torque is positive, the motor rotor deflects positively, and when the cogging torque is negative, the motor rotor deflects negatively. An anchor point is only formed between two deflection forces of equal magnitude and opposite direction. Therefore, P1 and P3 are the positioning points of the motor, while P2 cannot form the positioning point.
[0028] Based on the above cogging torque positioning principle, the positive and negative electromagnetic torque distributed along the circumference of the motor axis section...
PUM
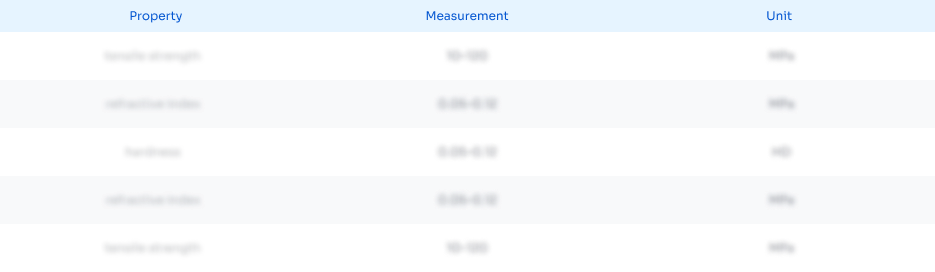
Abstract
Description
Claims
Application Information

- R&D Engineer
- R&D Manager
- IP Professional
- Industry Leading Data Capabilities
- Powerful AI technology
- Patent DNA Extraction
Browse by: Latest US Patents, China's latest patents, Technical Efficacy Thesaurus, Application Domain, Technology Topic, Popular Technical Reports.
© 2024 PatSnap. All rights reserved.Legal|Privacy policy|Modern Slavery Act Transparency Statement|Sitemap|About US| Contact US: help@patsnap.com