Textile fabric processing system and processing method
A technology for textile fabrics and processing systems, applied in the field of textile fabric processing, can solve the problems that textile fabrics are easily contaminated with dust, affect the aesthetics of textile fabrics, reduce product quality, etc., so as to improve flatness and cleanliness, improve production and processing efficiency, The effect of improving product quality
- Summary
- Abstract
- Description
- Claims
- Application Information
AI Technical Summary
Problems solved by technology
Method used
Image
Examples
specific Embodiment approach 1
[0036] Such as Figure 1-14As shown, a textile fabric processing system includes a servo motor 1, a fabric dust removal mechanism 2, a cloth guide roller 3, a dust removal box 4, a sliding box door 5, a tension roller 6, a linkage frame 7, an ironing roller 8, a suction Dust mechanism 9, frame plate 10 and support leg 11, described servomotor 1 is fixedly connected on the frame plate 10 by motor seat; Described servomotor 1 transmission connects fabric dedusting mechanism 2; Described fabric dedusting mechanism 2 rotates and cooperates Connected to the middle part inside the dust removal box 4; the dust removal box 4 is fixedly connected to the frame plate 10; the four corners of the bottom surface of the frame plate 10 are respectively fixedly connected to a support leg 11; The top and bottom surfaces of the dust removal box 4 are all hollow structures; the top of the dust removal box 4 is slidingly fitted to connect the sliding door 5; the lower end of the front side of the ...
specific Embodiment approach 2
[0038] Such as Figure 1-14 As shown, the fabric dust removal mechanism 2 includes an upper shaft 2-1, a dust removal roller brush 2-2, a lower shaft 2-3, a driving gear 2-4, a driven gear 2-5, a transmission pulley 2-6 and a transmission sprocket 2-7; the upper rotating shaft 2-1 and the lower rotating shaft 2-3 are respectively rotated and connected to the upper and lower sides of the middle part of the dust removal box 4; the middle parts of the upper rotating shaft 2-1 and the lower rotating shaft 2-3 are respectively fixedly connected to one Dust removal roller brush 2-2, two dust removal roller brushes 2-2 are all rotatably connected in the dust removal box 4; The upper shaft 2-1 is connected to the output shaft of the servo motor 1 through a coupling; The upper shaft 2-1 The two ends of the drive gear 2-4 and the drive pulley 2-6 are respectively fixedly connected; the two ends of the lower rotating shaft 2-3 are respectively fixedly connected with the driven gear 2-5 a...
specific Embodiment approach 3
[0040] Such as Figure 1-14 As shown, the inner and outer ends of the sliding box door 5 are respectively fixedly connected with a limit baffle, and the two limit baffles are respectively located at the inner and outer ends of the dust removal box 4 . The sliding box door 5 is sealed and slidably connected between the dust removal box 4, which is convenient for the dust suction mechanism 9 to absorb dust after the fabric is dedusted.
PUM
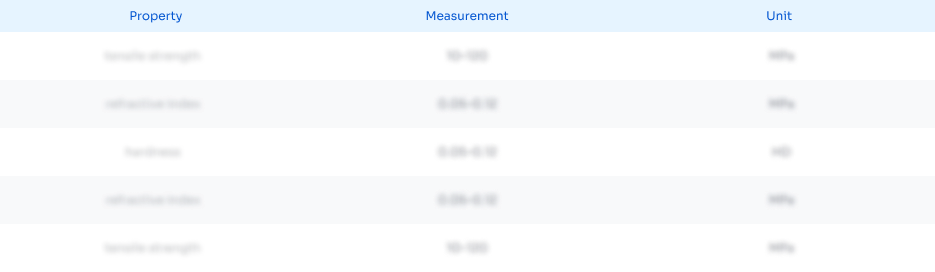
Abstract
Description
Claims
Application Information

- R&D
- Intellectual Property
- Life Sciences
- Materials
- Tech Scout
- Unparalleled Data Quality
- Higher Quality Content
- 60% Fewer Hallucinations
Browse by: Latest US Patents, China's latest patents, Technical Efficacy Thesaurus, Application Domain, Technology Topic, Popular Technical Reports.
© 2025 PatSnap. All rights reserved.Legal|Privacy policy|Modern Slavery Act Transparency Statement|Sitemap|About US| Contact US: help@patsnap.com