No in boiler flue gas x Partial redox removal method and removal device
A boiler flue gas removal technology, which is applied in separation methods, chemical instruments and methods, gas treatment, etc., can solve the problems of poor reduction effect, hindering industrial application, and difficulty in controlling the degree of oxidation, etc., and achieves strong high temperature resistance and corrosion resistance , Visible light catalytic activity is strong, the effect of reducing oxidation residence time
- Summary
- Abstract
- Description
- Claims
- Application Information
AI Technical Summary
Problems solved by technology
Method used
Image
Examples
Embodiment 1
[0053] (1) Photocatalytic oxidation: The boiler flue gas enters the two-stage photocatalytic oxidation device in series respectively, and the photocatalytic oxidation is carried out in sequence. The first-stage photocatalytic oxidation device is equipped with three mesh plates loaded with photocatalysts along the gas flow direction ; In the second-stage photocatalytic oxidation device, there are two loaded nano-Pd / TiO along the direction of gas flow. 2 50W LED lights are arranged between the mesh panels. The residence time of boiler flue gas in the first-stage photocatalytic oxidation device is 15s; the residence time of boiler flue gas in the second-stage photocatalytic oxidation device is 10s. NO in the flue gas after the first stage photocatalytic oxidation X The degree of oxidation is 75%, and the NO in the flue gas after the second stage photocatalytic oxidation X The degree of oxidation is 50%. According to the inlet oxidation degree and outlet gas oxidation degree of...
Embodiment 2
[0058] (1) Photocatalytic oxidation: The boiler flue gas enters the two-stage photocatalytic oxidation device in series respectively, and the photocatalytic oxidation is carried out in sequence. The first-stage photocatalytic oxidation device is equipped with three mesh plates loaded with photocatalysts along the gas flow direction ; In the second-stage photocatalytic oxidation device, there are two loaded nano-Pd / TiO along the direction of gas flow. 2 50W LED lights are arranged between the mesh panels. The residence time of boiler flue gas in the first-stage photocatalytic oxidation device is 18s; the residence time of boiler flue gas in the second-stage photocatalytic oxidation device is 12s. NO in the flue gas after the first stage photocatalytic oxidation X The degree of oxidation is 80%, and the NO in the flue gas after the second stage photocatalytic oxidation X The degree of oxidation is 49%. According to the inlet oxidation degree and outlet gas oxidation degree of...
Embodiment 3
[0063] (1) Photocatalytic oxidation: The boiler flue gas enters the two-stage photocatalytic oxidation device in series respectively, and the photocatalytic oxidation is carried out in sequence. The first-stage photocatalytic oxidation device is equipped with three mesh plates loaded with photocatalysts along the gas flow direction ; In the second-stage photocatalytic oxidation device, there are two loaded nano-Pd / TiO along the direction of gas flow.2 50W LED lights are arranged between the mesh panels. The residence time of boiler flue gas in the first-stage photocatalytic oxidation device is 10s; the residence time of boiler flue gas in the second-stage photocatalytic oxidation device is 8s. NO in the flue gas after the first stage photocatalytic oxidation X The degree of oxidation is 70%, and the NO in the flue gas after the second stage photocatalytic oxidation X The degree of oxidation is 50%. According to the inlet oxidation degree and outlet gas oxidation degree of ea...
PUM
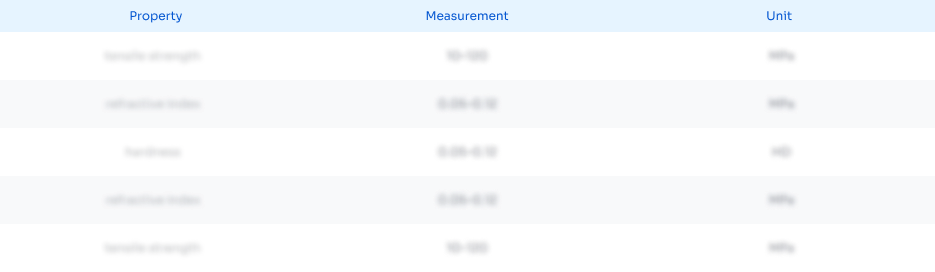
Abstract
Description
Claims
Application Information

- R&D
- Intellectual Property
- Life Sciences
- Materials
- Tech Scout
- Unparalleled Data Quality
- Higher Quality Content
- 60% Fewer Hallucinations
Browse by: Latest US Patents, China's latest patents, Technical Efficacy Thesaurus, Application Domain, Technology Topic, Popular Technical Reports.
© 2025 PatSnap. All rights reserved.Legal|Privacy policy|Modern Slavery Act Transparency Statement|Sitemap|About US| Contact US: help@patsnap.com