Cable-free linear motor feeding system
A linear motor and feed system technology, applied in metal processing machinery parts, large fixed members, maintenance and safety accessories, etc., can solve the problems of limiting the running speed and positioning accuracy of the system, and improve the running speed and positioning accuracy. , The effect of preventing pollution and uniform heat dissipation
- Summary
- Abstract
- Description
- Claims
- Application Information
AI Technical Summary
Problems solved by technology
Method used
Image
Examples
Embodiment 1
[0029] Such as figure 1 As shown, the cable-free linear motor feeding system includes a marble base 1, a load assembly 2, a linear motor mover 3, a linear motor stator 4, a water cooling plate 5, a position signal detection assembly 6 and a controller.
[0030] The marble base 1 has a main groove and a side groove, and the side groove is used as an air bearing guide rail to support the movement of the load assembly 2, and the three surfaces of the side groove are provided with throttle holes, such as Figure 4 shown. Anti-collision buffer pieces are installed at both ends of the side slot. The load assembly 2 is also made of marble, and is inserted longitudinally into the side groove of the marble base. There are 6 threaded holes on the upper surface of the load component 2 for connecting with the load. A protective cover can be installed on the upper surface of the load assembly to prevent waste chips from production and processing from entering the air flotation working s...
PUM
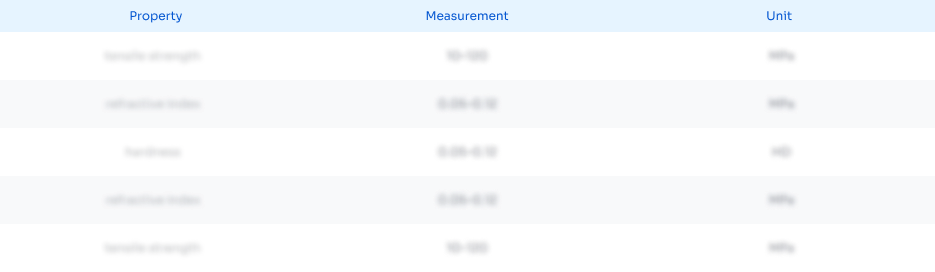
Abstract
Description
Claims
Application Information

- R&D Engineer
- R&D Manager
- IP Professional
- Industry Leading Data Capabilities
- Powerful AI technology
- Patent DNA Extraction
Browse by: Latest US Patents, China's latest patents, Technical Efficacy Thesaurus, Application Domain, Technology Topic, Popular Technical Reports.
© 2024 PatSnap. All rights reserved.Legal|Privacy policy|Modern Slavery Act Transparency Statement|Sitemap|About US| Contact US: help@patsnap.com