A PD/MC redispersed by PD x Supported catalyst and its preparation method and application
A supported catalyst and redispersion technology, which is applied in physical/chemical process catalysts, dehalogenation preparation, chemical instruments and methods, etc., can solve the problems of unenvironmental atmosphere, low efficiency, and unsatisfactory catalyst activity recovery, and achieve production costs. Low, simple preparation method, excellent selectivity effect
- Summary
- Abstract
- Description
- Claims
- Application Information
AI Technical Summary
Problems solved by technology
Method used
Image
Examples
Embodiment 1
[0025] 1 g of fresh Pd / FeC with a Pd loading of 3% x The catalyst was loaded into a fixed-bed reactor, fed with hydrogen and reduced at 250°C for 2 hours. Then feed CFC-115 gas at a reaction temperature of 300°C and a space velocity of 720h -1 The reaction is carried out under the conditions, and the feed molar ratio of CFC-115 raw material to hydrogen is 1:1.5. After 80 hours of reaction, when the conversion rate of CFC-115 is lower than 65%, it is recorded as the sintering deactivation of the catalyst.
[0026] The catalyst deactivated by sintering in O with an oxygen volume content of 8% 2 / N 2 Pd / FeO was obtained by calcination at 450℃ for 0.5h x catalyst, and then 10% CH at 300°C 4 / H 2 Gas mixture (i.e. CH 4 / H 2 In the gas mixture, CH 4 The volume content is 10%) calcined and carbonized for 1h to recover Pd / FeC x The activity of the catalyst, that is, the regenerated catalyst is obtained. Under the same reaction conditions, the hydrodechlorination reaction of...
Embodiment 2
[0029] 1 g of fresh Pd / FeC with a Pd loading of 9% x The catalyst was loaded into a fixed-bed reactor, fed with hydrogen and reduced at 250°C for 2 hours. Then feed CFC-115 gas at a reaction temperature of 300°C and a space velocity of 720h -1 The reaction is carried out under the conditions, and the feed molar ratio of CFC-115 raw material to hydrogen is 1:1.5. After 80 hours of reaction, when the conversion rate of CFC-115 is lower than 65%, it is recorded as the sintering deactivation of the catalyst.
[0030] The catalyst deactivated by sintering in O with an oxygen volume content of 16% 2 / N 2atmosphere and calcination at 400°C for 8h to obtain Pd / FeO x catalyst, and then 20% CH at 650°C 4 / H 2 Restoration of Pd / FeC by Mixed Gas Calcination and Carbonization for 10h x The activity of the catalyst, that is, the regenerated catalyst is obtained. Under the same conditions, the hydrodechlorination reaction of CFC-115 under the action of the regenerated catalyst was ca...
Embodiment 3
[0033] 1 g of fresh Pd / FeC with a Pd loading of 5% x The catalyst was loaded into a fixed-bed reactor, fed with hydrogen and reduced at 250°C for 2 hours. Then feed CFC-115 gas at a reaction temperature of 300°C and a space velocity of 720h -1 The reaction is carried out under the conditions, and the feed molar ratio of CFC-115 raw material to hydrogen is 1:1.5. After 80 hours of reaction, when the conversion rate of CFC-115 is lower than 65%, it is recorded as the sintering deactivation of the catalyst.
[0034] The catalyst deactivated by sintering in O with an oxygen volume content of 6% 2 / N 2 atmosphere and calcination at 500°C for 1 h to obtain Pd / FeO x Catalyst, and then calcination and carbonization at 300 °C for 3 h to recover Pd / FeC x The activity of the catalyst, that is, the regenerated catalyst is obtained. Under the same conditions, the hydrodechlorination reaction of CFC-115 under the action of the regenerated catalyst was carried out again.
[0035] When...
PUM
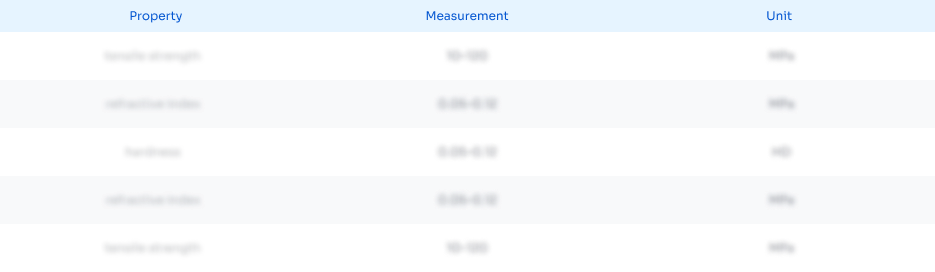
Abstract
Description
Claims
Application Information

- R&D Engineer
- R&D Manager
- IP Professional
- Industry Leading Data Capabilities
- Powerful AI technology
- Patent DNA Extraction
Browse by: Latest US Patents, China's latest patents, Technical Efficacy Thesaurus, Application Domain, Technology Topic, Popular Technical Reports.
© 2024 PatSnap. All rights reserved.Legal|Privacy policy|Modern Slavery Act Transparency Statement|Sitemap|About US| Contact US: help@patsnap.com