Blast furnace molten iron quality predicting system based on ensemble learning and method
A blast furnace hot metal and quality prediction technology, applied in the blast furnace, blast furnace details, chemical statistics, etc., can solve the problems of long calculation time of the soft sensor model, inability to fully reflect the complex state inside the blast furnace, and low efficiency
- Summary
- Abstract
- Description
- Claims
- Application Information
AI Technical Summary
Problems solved by technology
Method used
Image
Examples
Embodiment Construction
[0073] The invention will be further described below in conjunction with the accompanying drawings and specific implementation examples. The present invention proposes a blast furnace molten iron quality prediction system and method based on integrated learning; specifically, a blast furnace molten iron quality prediction system based on integrated learning, such as figure 1 As shown, including: blast furnace 1, hot blast stove 2, first flowmeter 3-1, second flowmeter 3-2, third flowmeter 3-3, thermometer 4, pressure gauge 5, hygrometer 6, bosh gas Measurement analyzer 7, oxygen enrichment rate measurement analyzer 8, data acquisition device 9 and computer 10;
[0074] The ore, coke and solvent 11 to be tested are placed into the interior of the blast furnace 1 from the entrance of the blast furnace 1, and the pulverized coal is injected 12 from the tuyere of the blast furnace belly of the blast furnace 1, and the first flow meter 3-1 is installed at the pulverized coal injecti...
PUM
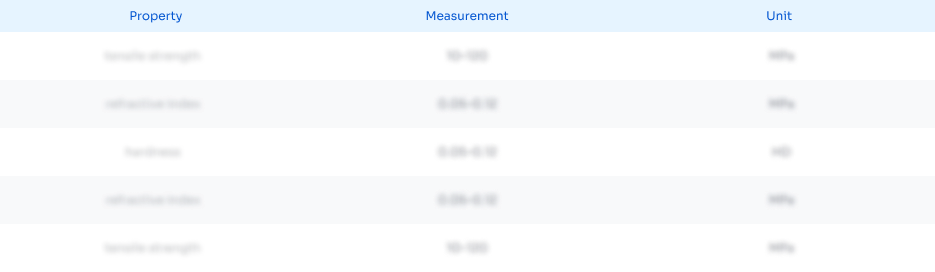
Abstract
Description
Claims
Application Information

- Generate Ideas
- Intellectual Property
- Life Sciences
- Materials
- Tech Scout
- Unparalleled Data Quality
- Higher Quality Content
- 60% Fewer Hallucinations
Browse by: Latest US Patents, China's latest patents, Technical Efficacy Thesaurus, Application Domain, Technology Topic, Popular Technical Reports.
© 2025 PatSnap. All rights reserved.Legal|Privacy policy|Modern Slavery Act Transparency Statement|Sitemap|About US| Contact US: help@patsnap.com