Pile driving barge and posture adjustment, positioning control and pile driving methods thereof
A technology for a piling ship and a piling device, which is used in attitude control, sheet pile wall, transportation and packaging, etc., can solve the problems of easy breaking, pile caps and hydraulic pile hammers falling into the sea, and safety problems, so as to avoid breaking. pile, the effect of improving safety and service life
- Summary
- Abstract
- Description
- Claims
- Application Information
AI Technical Summary
Problems solved by technology
Method used
Image
Examples
Embodiment Construction
[0153] Specific embodiments of the present invention will be described in detail below in conjunction with the accompanying drawings.
[0154] Such as Figure 1-8 And as shown in 38 and 39, a piling ship includes a hull 1, the four corners of the hull 1 are respectively provided with a buoyancy adjustment device, the lower surface of the deck 101 is connected with the buoyancy adjustment device, and the buoyancy adjustment device includes a buoyancy adjustment device arranged on the hull 1 The ballast water tank 18 and the connecting plate 17 provided on the lower surface of the deck 101, the connecting plate 17 is hinged with a propulsion device 182 arranged vertically downward, and the bottom of the ballast water tank 18 is provided with a through hole communicating with the outside world, The ballast water tank 18 is provided with a pressure water plate 181 on the liquid surface, and a sealing ring 185 is arranged between the pressure water plate 181 and the inner wall of t...
PUM
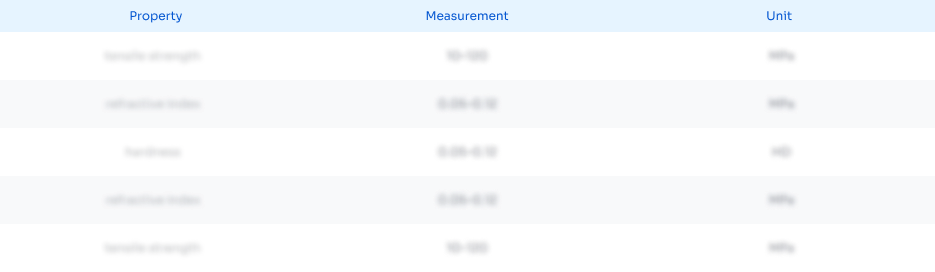
Abstract
Description
Claims
Application Information

- Generate Ideas
- Intellectual Property
- Life Sciences
- Materials
- Tech Scout
- Unparalleled Data Quality
- Higher Quality Content
- 60% Fewer Hallucinations
Browse by: Latest US Patents, China's latest patents, Technical Efficacy Thesaurus, Application Domain, Technology Topic, Popular Technical Reports.
© 2025 PatSnap. All rights reserved.Legal|Privacy policy|Modern Slavery Act Transparency Statement|Sitemap|About US| Contact US: help@patsnap.com