Resistance-type strain sensor and strain measurement method
A technology of resistive strain and strain sensors, applied in the direction of electric/magnetic solid deformation measurement, electromagnetic measurement devices, etc., can solve the problems of unsuitable long-term precision measurement, permanent damage or creep of microstructure, etc.
- Summary
- Abstract
- Description
- Claims
- Application Information
AI Technical Summary
Problems solved by technology
Method used
Image
Examples
Embodiment 1
[0073] Embodiment 1: It is an embodiment of the resistive strain sensor with the structure shown in FIG. 1 .
[0074] The thickness of the PI film of the strain sensor is 0.05 mm, the width of the PI film at the arc and straight line sections is 0.05 mm, the average radius is 0.15 mm, and the length of the straight line section is 0.15 mm. The thickness of the gold foil is 100nm, and the bonding layer chromium between the PI film and the PI film is 10nm. The line width of the gold foil in the curved section is 2μm and 2.25μm, which are respectively 0.015mm from the inner edge of PI and 0.015mm from the outer edge of PI; Same width as PI film. The length of the PI on both sides for pasting the measured object is 1.13mm, and the width is 0.4mm.
[0075] Preparation:
[0076] Purchase or spin-coat a polymer film as the substrate 1, and coat a layer of metal film on the substrate 1 to become a composite laminate;
[0077] Making a photolithographic master: cover a layer of phot...
Embodiment 2
[0079] Example 2: for image 3 An embodiment of a resistive strain sensor of the structure shown.
[0080] The thickness of the PI film of the strain sensor is 0.05 mm, the width of the PI film at the arc and straight line sections is 0.05 mm, the average radius is 0.15 mm, and the length of the straight line section is 0.15 mm. The thickness of the gold foil is 100nm, and the bonding layer chromium between the PI film and the PI film is 10nm. The line width of the gold foil in the curved section is 2μm and 2.25μm, which are respectively 0.015mm from the inner edge of PI and 0.015mm from the outer edge of PI; Same width as PI film. The length of the PI on both sides for pasting the measured object is 1.53mm, and the width is 0.4mm.
[0081] Preparation:
[0082] Purchase or spin-coat a polymer film as the substrate 1, and coat a layer of metal film on the substrate 1 to become a composite laminate;
[0083] Making a photolithographic master: cover a layer of photoresist on...
PUM
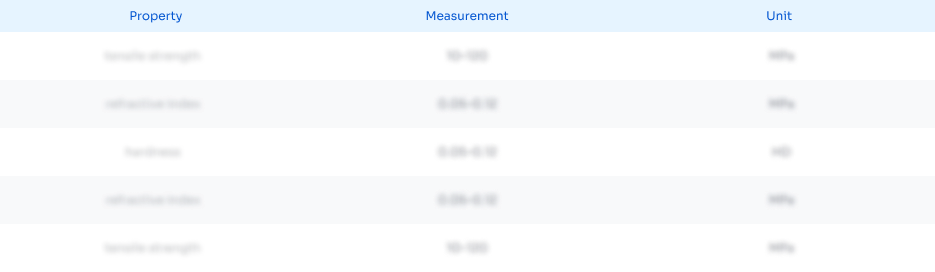
Abstract
Description
Claims
Application Information

- R&D
- Intellectual Property
- Life Sciences
- Materials
- Tech Scout
- Unparalleled Data Quality
- Higher Quality Content
- 60% Fewer Hallucinations
Browse by: Latest US Patents, China's latest patents, Technical Efficacy Thesaurus, Application Domain, Technology Topic, Popular Technical Reports.
© 2025 PatSnap. All rights reserved.Legal|Privacy policy|Modern Slavery Act Transparency Statement|Sitemap|About US| Contact US: help@patsnap.com