Enhanced paper pulp molding production method
A technology of pulp molding and production methods, applied in neural learning methods, papermaking, 3D modeling, etc., can solve problems such as large fluctuations in product quality, poor fiber strength and toughness, and poor fluidity
- Summary
- Abstract
- Description
- Claims
- Application Information
AI Technical Summary
Problems solved by technology
Method used
Image
Examples
preparation example Construction
[0116] In step S103, the preparation method of the pulp fiber provided by the embodiment of the present invention includes:
[0117] (1) The eucalyptus wood raw material is peeled and chipped to become wood chips, and sent to a negative pressure mixing bin with a temperature of 55±5°C and a pressure below -10kpa for decompression and exhaust for 10 to 15 minutes; Under the state, excessively add the cooking agent and keep it for 45-50 minutes; then return to the normal temperature and pressure state, and discharge the excess cooking agent.
[0118] (2) Send the wood chips treated in step (1) into the cooking equipment according to the conventional cooking curve to raise the temperature for 95-100 minutes, the highest temperature is 145-155 ° C, and keep warm for 160-170 minutes for cooking. After the cooking is completed, spray the slurry. Washing, sorting and sieving are carried out as usual to obtain good pulp and black liquor, and the black liquor enters the alkali recovery...
Embodiment 1
[0129] The enhanced pulp molding provided by the invention is used to produce disposable paper cups, and the operation process is as follows:
[0130] Determine the design parameters of pulp molding and set the production parameters of pulp molding.
[0131] The three-dimensional model of the disposable paper cup of the pulp molded product is designed by using the three-dimensional design software.
[0132] Use conveying equipment to convey pulp fiber, water and polyacrylamide resin solution.
[0133] Use a mixer to stir and mix the input raw materials, use a continuous drying furnace to pass through different temperature zones, and dry until the moisture content drops to about 10% to 12%.
[0134] The thermocompression molding operation is performed according to the designed three-dimensional model of the pulp molded product using thermocompression molding equipment.
[0135] The device display can display and store a 3D model of the designed pulp molded product.
[0136] ...
Embodiment 2
[0144] Production step is the same as embodiment 1, and the preparation method difference of pulp fiber is: the NaOH concentration is adjusted to 3.9% in the cooking agent of step (1). The cooking equipment in step (2) is a batch cooker without liquid medicine circulation.
PUM
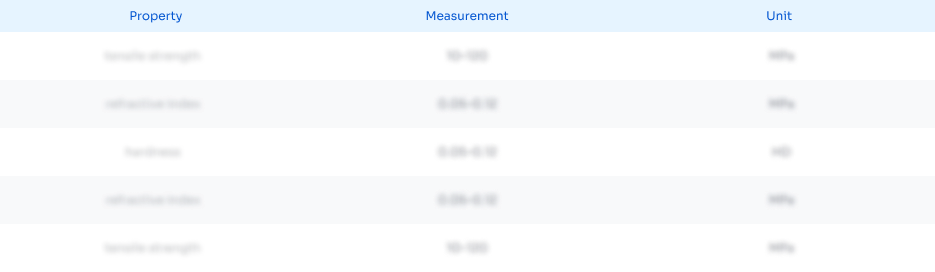
Abstract
Description
Claims
Application Information

- Generate Ideas
- Intellectual Property
- Life Sciences
- Materials
- Tech Scout
- Unparalleled Data Quality
- Higher Quality Content
- 60% Fewer Hallucinations
Browse by: Latest US Patents, China's latest patents, Technical Efficacy Thesaurus, Application Domain, Technology Topic, Popular Technical Reports.
© 2025 PatSnap. All rights reserved.Legal|Privacy policy|Modern Slavery Act Transparency Statement|Sitemap|About US| Contact US: help@patsnap.com