Halogen-free flame retardant, preparation method thereof, and cable tray comprising the halogen-free flame retardant
A cable tray and flame retardant technology, which is applied in the field of halogen-free flame retardants and cable trays, can solve problems such as high smoke density, poor thermal stability, and corrosion
- Summary
- Abstract
- Description
- Claims
- Application Information
AI Technical Summary
Problems solved by technology
Method used
Image
Examples
preparation example Construction
[0030] On the other hand, another embodiment of the present invention provides a preparation method of the above-mentioned halogen-free flame retardant, the preparation method comprising the following steps:
[0031] Exfoliate the vermiculite to obtain vermiculite with fully exfoliated layer structure;
[0032] The graphene is intercalated between the layers of the exfoliated vermiculite to obtain the halogen-free flame retardant.
[0033] The process of exfoliating vermiculite is also the process of increasing the interlayer spacing of vermiculite. Therefore, in this embodiment, the method for exfoliating the vermiculite is not particularly limited, as long as the effect can be achieved. In a preferred example, the method for exfoliating the vermiculite includes: dispersing the vermiculite in deionized water and ultrasonicating to obtain the vermiculite whose layer structure is fully exfoliated. Wherein, the power of the ultrasonic wave is preferably above 1000W, at this ti...
Embodiment 1
[0045] A preparation method of a halogen-free flame retardant, comprising the steps of:
[0046]Disperse 3 g of vermiculite into 300 ml of deionized water, stir for 2 hours, and peel off for 5 hours with an ultrasonic cell pulverizer, wherein the peeling power is 1000 W to obtain a vermiculite dispersion. Disperse 7 g of graphene into 200 ml of deionized water, and ultrasonically stir for 1 h to obtain a graphene dispersion. The graphene dispersion and the vermiculite dispersion were mixed and ultrasonically stirred for 5 hours, and then subjected to vacuum filtration to obtain a halogen-free flame retardant for graphene-intercalated vermiculite. Its XRD spectrum is as figure 1 As shown, it can be seen from the figure that compared with the characteristic peak of vermiculite, the characteristic peak of the vermiculite halogen-free flame retardant intercalated with graphene shifts to the left, from 7.2° to 2.79°, and can be calculated according to the Bragg equation , Vermicu...
Embodiment 2
[0048] A preparation method of a halogen-free flame retardant, comprising the steps of:
[0049] Disperse 3 g of vermiculite into 300 ml of deionized water, stir for 2 hours, and peel off for 5 hours with an ultrasonic cell pulverizer, wherein the peeling power is 1200 W to obtain a vermiculite dispersion. Disperse 0.75 g of graphene into 200 ml of deionized water, and ultrasonically stir for 1 h to obtain a graphene dispersion. The graphene dispersion and the vermiculite dispersion were mixed and ultrasonically stirred for 5 hours, and then subjected to vacuum filtration to obtain a graphene-intercalated vermiculite halogen-free flame retardant.
PUM
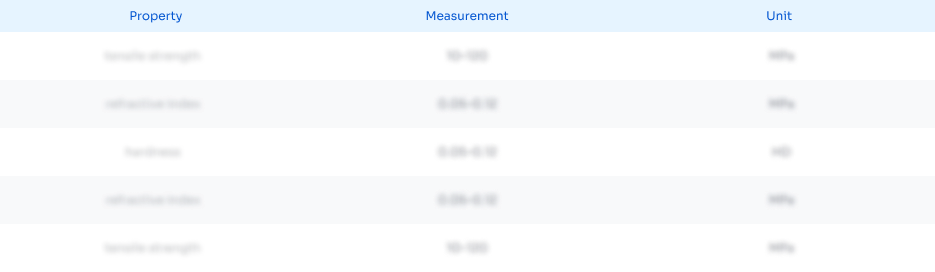
Abstract
Description
Claims
Application Information

- R&D Engineer
- R&D Manager
- IP Professional
- Industry Leading Data Capabilities
- Powerful AI technology
- Patent DNA Extraction
Browse by: Latest US Patents, China's latest patents, Technical Efficacy Thesaurus, Application Domain, Technology Topic, Popular Technical Reports.
© 2024 PatSnap. All rights reserved.Legal|Privacy policy|Modern Slavery Act Transparency Statement|Sitemap|About US| Contact US: help@patsnap.com