A robotic finger mechanism
A technology of robot fingers and bases, applied in the field of robots, can solve the problems of complex structure, difficult to meet the requirements of small operation space of robot fingers, and large volume.
- Summary
- Abstract
- Description
- Claims
- Application Information
AI Technical Summary
Problems solved by technology
Method used
Image
Examples
Embodiment 1
[0024] Such as figure 1 As shown, this embodiment provides a robot finger mechanism, including a machine base 1, a screw motor 2, a screw nut 3, a guide sleeve 4, a finger frame 5, a spring leaf 6, a spring rod group, a force measuring rod group and a soft finger The base 1 is a cylindrical base, the base 1 is provided with a first through hole, an axial groove and a first threaded hole, the first through hole is coaxial with the base 1, and the first threaded hole is perpendicular to the base 1 The screw motor 2 includes a motor and a screw, the output end of the motor is connected with the screw, the screw nut 3 is a rectangular parallelepiped screw nut, and the screw nut 3 is provided with a first threaded through hole and a left side parallel to each other. The axis of the eccentric through hole and the right eccentric through hole, the axis of the left eccentric through hole and the right eccentric through hole are all perpendicular to the axis of the first threaded throu...
PUM
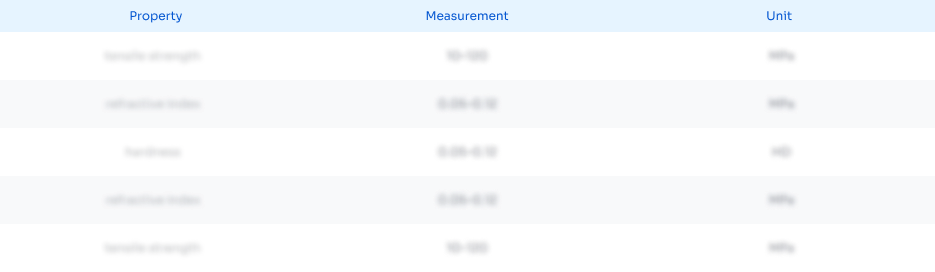
Abstract
Description
Claims
Application Information

- R&D
- Intellectual Property
- Life Sciences
- Materials
- Tech Scout
- Unparalleled Data Quality
- Higher Quality Content
- 60% Fewer Hallucinations
Browse by: Latest US Patents, China's latest patents, Technical Efficacy Thesaurus, Application Domain, Technology Topic, Popular Technical Reports.
© 2025 PatSnap. All rights reserved.Legal|Privacy policy|Modern Slavery Act Transparency Statement|Sitemap|About US| Contact US: help@patsnap.com