Large-variable-diameter thin-wall pipe composite forming device
A technology for composite forming and thin-walled tubes, which is applied in the field of composite forming devices for large variable-diameter thin-walled tubes, can solve the problems of high scrap rate, low production efficiency, easy cracking and wrinkling, etc., and achieve low cost and high work efficiency , Improve the effect of practicality and economy
- Summary
- Abstract
- Description
- Claims
- Application Information
AI Technical Summary
Problems solved by technology
Method used
Image
Examples
Embodiment 1
[0028] A compound forming device for large-diameter thin-walled pipes, such as figure 1 As shown, it includes a frame 1, a first motor 2, a transmission device 3, a transmission shaft 4, a first bearing seat 5, a support plate 6, a first clamping device 7, a first push-pull device 8, a connecting plate 9, a first Two clamping devices 10, the second push-pull device 12, the first connecting frame 13, the first rotating shaft 14, the preforming roller 15, the third pushing-pull device 16, the second connecting frame 17, the second rotating shaft 18 and the shaping roller 19, machine The bottom of the frame 1 is fixedly installed with a first motor 2, the output end of the first motor 2 is connected with a transmission device 3, the output end of the transmission device 3 is connected with a transmission shaft 4, and the other end of the transmission shaft 4 is fixedly connected with a first clamping device 7, the transmission The first bearing seat 5 is installed on the shaft 4,...
Embodiment 2
[0031] A compound forming device for large-diameter thin-walled pipes, such as Figure 1-Figure 2 As shown, it includes a frame 1, a first motor 2, a transmission device 3, a transmission shaft 4, a first bearing seat 5, a support plate 6, a first clamping device 7, a first push-pull device 8, a connecting plate 9, a first Two clamping devices 10, the second push-pull device 12, the first connecting frame 13, the first rotating shaft 14, the preforming roller 15, the third pushing-pull device 16, the second connecting frame 17, the second rotating shaft 18 and the shaping roller 19, machine The bottom of the frame 1 is fixedly installed with a first motor 2, the output end of the first motor 2 is connected with a transmission device 3, the output end of the transmission device 3 is connected with a transmission shaft 4, and the other end of the transmission shaft 4 is fixedly connected with a first clamping device 7, the transmission The first bearing seat 5 is installed on th...
PUM
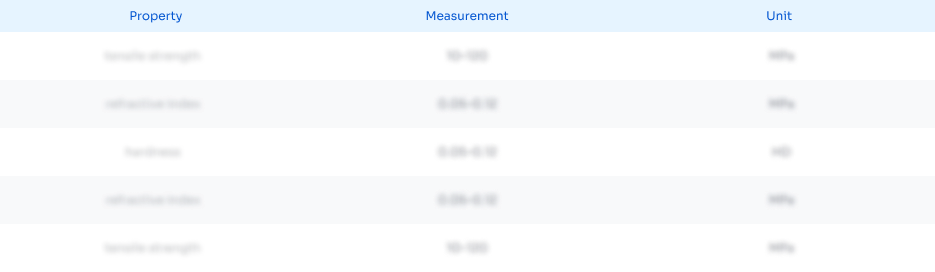
Abstract
Description
Claims
Application Information

- R&D
- Intellectual Property
- Life Sciences
- Materials
- Tech Scout
- Unparalleled Data Quality
- Higher Quality Content
- 60% Fewer Hallucinations
Browse by: Latest US Patents, China's latest patents, Technical Efficacy Thesaurus, Application Domain, Technology Topic, Popular Technical Reports.
© 2025 PatSnap. All rights reserved.Legal|Privacy policy|Modern Slavery Act Transparency Statement|Sitemap|About US| Contact US: help@patsnap.com