Method for preparing silicon vanadium nitride
A technology of silicon vanadium nitride and vanadium pentoxide, applied in the field of alloy smelting, can solve the problems of high production cost, high residual oxygen content, incomplete reaction, etc., achieve short production time, good alloying effect, and low equipment requirements Effect
- Summary
- Abstract
- Description
- Claims
- Application Information
AI Technical Summary
Problems solved by technology
Method used
Image
Examples
Embodiment 1
[0036] (1) Take vanadium pentoxide 20g, silicon dioxide 0.5g, carbon black 5.4g, mix and briquette;
[0037] (2) Put the pressed sample in step (1) into a high-temperature furnace, heat to 1400° C. under a nitrogen atmosphere, and keep it warm for 5 hours; the product silicon vanadium nitride is obtained after the reaction is completed.
[0038] The test results show that the vanadium content in the product is 76.1%, the silicon content is 1.4%, and the nitrogen content is 17.6%.
Embodiment 2
[0040] (1) Take vanadium pentoxide 20g, silicon dioxide 3g, carbon black 6.3g, mix and briquette;
[0041] (2) Put the materials in the step (1) into a high-temperature furnace, heat to 1500° C. under a nitrogen atmosphere, and keep the temperature for 4 hours; after the reaction, the product silicon vanadium nitride is obtained.
[0042] The test results show that the vanadium content in the product is 67.3%, the silicon content is 8.2%, and the nitrogen content is 20.8%.
[0043] figure 1 It is the XRD pattern of the silicon nitride vanadium product obtained in embodiment 2, as can be seen from the figure, the main composition of product is VN and Si 3 N 4 , silicon to Si 3 N 4 Exist in the form of , greatly improve the nitrogen content of the product.
Embodiment 3
[0045] (1) Take vanadium pentoxide 20g, silicon dioxide 4g, carbon black 6.8g, mix and briquette;
[0046] (2) Put the materials in the step (1) into a high-temperature furnace, heat to 1600° C. under a nitrogen atmosphere, and keep the temperature for 3 hours; after the reaction, the product silicon vanadium nitride is obtained.
[0047] The test results show that the vanadium content in the product is 64.3%, the silicon content is 10.6%, and the nitrogen content is 22.6%.
PUM
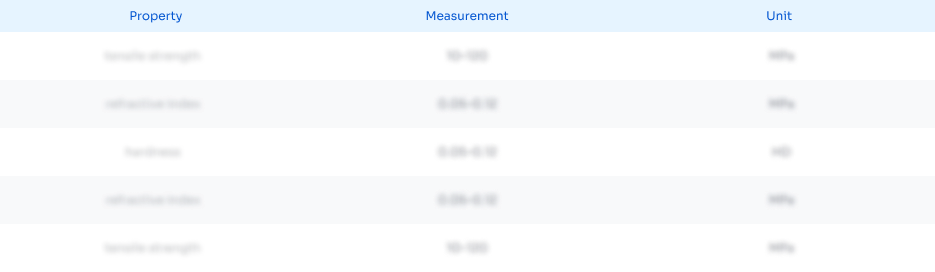
Abstract
Description
Claims
Application Information

- R&D
- Intellectual Property
- Life Sciences
- Materials
- Tech Scout
- Unparalleled Data Quality
- Higher Quality Content
- 60% Fewer Hallucinations
Browse by: Latest US Patents, China's latest patents, Technical Efficacy Thesaurus, Application Domain, Technology Topic, Popular Technical Reports.
© 2025 PatSnap. All rights reserved.Legal|Privacy policy|Modern Slavery Act Transparency Statement|Sitemap|About US| Contact US: help@patsnap.com