Preparation method for low-silicon, high-calcium and large-crystal fused magnesia
A technology of fused magnesia and crystallization, which is applied in the field of fused magnesia production, can solve problems such as high ash content, volatile matter, and impurity content, which affect the output rate of fused magnesia, and broken electrodes are not easy to break, reaching the added amount Easy to control, significant marketing value, and the effect of reducing the calcination temperature
- Summary
- Abstract
- Description
- Claims
- Application Information
AI Technical Summary
Problems solved by technology
Method used
Image
Examples
Embodiment 1
[0017] Example 1: Preparation of a low-silicon, high-calcium, large-crystal fused magnesia
[0018] (1) Preparation of highly active MgO: Select 1000kg of magnesite with a block size of 100-200mm and MgO content exceeding 45%, and place it in a light-fired kiln for continuous calcination at 900°C for 4 hours. During the calcination process, add concentration 5% Na 2 CO 3 Solution 80kg, after the calcination, the obtained product is pulverized and ground to 200-300 mesh, and the high-activity MgO powder can be obtained;
[0019] (2) Electric arc furnace smelting: Take 900kg of high-activity MgO powder, add 9kg of high-purity graphite powder as a reducing agent, stir evenly and press the ball, place it in a fully automatic electric melting electric arc furnace at 2800 ° C for 8 hours, At the end of smelting, carry out insulation cooling and crystallization for 6 days, and then classify and crush to obtain low-silicon, high-calcium and large-crystal fused magnesia.
Embodiment 2
[0020] Example 2: Preparation of a low-silicon, high-calcium, large-crystal fused magnesia
[0021] (1) Preparation of highly active MgO: Select 1000kg of magnesite with a block size of 100-200mm and MgO content exceeding 45%, and place it in a light-fired kiln for continuous calcination at 1000°C for 4 hours. During the calcination process, add concentration 12.5% Na 2 CO 3 Solution 55kg, after the calcination is finished, the obtained product is pulverized and ground to 200-300 mesh, and the high-activity MgO powder that can be obtained is obtained;
[0022] (2) Electric arc furnace smelting: Take 900kg of high-activity MgO powder, add 27kg of high-purity graphite powder as a reducing agent, stir evenly and press the ball, place it in a fully automatic electric melting electric arc furnace, and continue smelting with electricity at 3000°C for 6.5 hours. At the end of smelting, carry out insulation cooling and crystallization for 8 days, and then classify and crush to obt...
Embodiment 3
[0023] Example 3: Preparation of a low-silicon, high-calcium, large-crystal fused magnesia
[0024] (1) Preparation of highly active MgO: Select 1000kg of magnesite with a block size of 100-200mm and MgO content exceeding 45%, and place it in a light-fired kiln for continuous calcination at 1100°C for 4 hours. During the calcination process, add concentration 20% Na 2 CO 3 30kg of solution, after the calcination, the obtained product is pulverized and ground to 200-300 mesh, and the high-activity MgO powder can be obtained;
[0025] (2) Electric arc furnace smelting: Take 900kg of high-activity MgO powder, add 45kg of high-purity graphite powder as a reducing agent, stir evenly and press the ball, place it in a fully automatic electric melting electric arc furnace at 3200 ° C for 8 hours, At the end of smelting, carry out insulation cooling and crystallization for 10 days, and then classify and crush to obtain low-silicon, high-calcium and large-crystal fused magnesia.
PUM
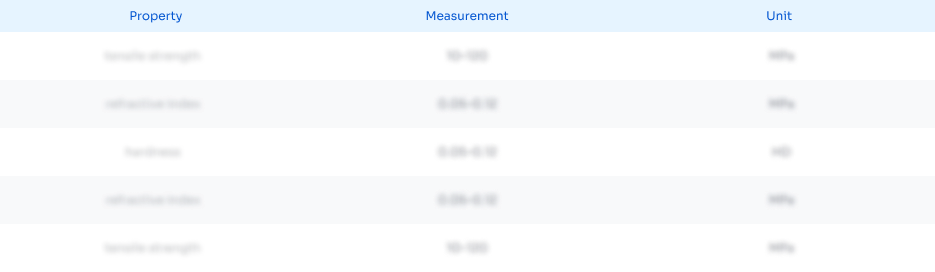
Abstract
Description
Claims
Application Information

- Generate Ideas
- Intellectual Property
- Life Sciences
- Materials
- Tech Scout
- Unparalleled Data Quality
- Higher Quality Content
- 60% Fewer Hallucinations
Browse by: Latest US Patents, China's latest patents, Technical Efficacy Thesaurus, Application Domain, Technology Topic, Popular Technical Reports.
© 2025 PatSnap. All rights reserved.Legal|Privacy policy|Modern Slavery Act Transparency Statement|Sitemap|About US| Contact US: help@patsnap.com