A high-precision method for measuring interface contact thermal resistance by bidirectional heat flow method
A technology of contact thermal resistance and heat flow method, which is applied in the field of testing, can solve problems such as not being perfect, and achieve the effects of improving test accuracy, facilitating thermal protection treatment, and realizing one-dimensional heat conduction
- Summary
- Abstract
- Description
- Claims
- Application Information
AI Technical Summary
Problems solved by technology
Method used
Image
Examples
Embodiment 1
[0037] The high-precision test method for measuring the interface contact thermal resistance by the bidirectional heat flow method of the present invention, the specific steps are as follows:
[0038] The first step, the preparation of the test equipment:
[0039] The upper and lower pairs of samples to be tested (the lower sample pair is sample 1 and sample 2, and the upper sample pair is sample 3 and sample 4) are vertically installed on the center of the heating body symmetrically up and down. Between the two set refrigeration blocks, the heating body is arranged in the middle position, in order to accurately obtain the heat flow value, four heat flow meters are added between the upper and lower two sample pairs and the heating body and the refrigeration block;
[0040] The structure diagram of the test device of the present invention is as follows figure 1As shown in the figure, the test device is similar to the American national standard ASTM E1225, and it has been furth...
Embodiment 2
[0058] The imaging of the upper sample pair (sample 3 and sample 4) and its temperature data processing method are as follows: Figure 4 shown. Specifically, the size of the captured temperature field image is as follows: Figure 4 a, the image is 512 pixels (the axial direction of the sample to be tested is the longitudinal direction) × 640 pixels (the cross-sectional direction of the sample to be tested is the horizontal direction), and the corresponding actual size is about 5120 μm × 6400 μm, Figure 4 In a, from top to bottom are the upper heat flow meter, sample material 3 and sample material 4. In order to improve the value accuracy of the interface temperature difference and heat flow, the Figure 4 The image is extracted at the contact interface of a, and the extracted image is 90 pixels (the axial direction of the sample to be tested) × 100 pixels (the direction of the cross-section of the sample to be tested). Figure 4 b, The temperature distribution at the conta...
PUM
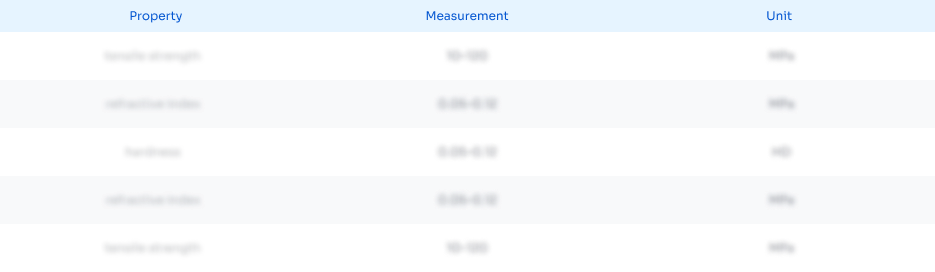
Abstract
Description
Claims
Application Information

- Generate Ideas
- Intellectual Property
- Life Sciences
- Materials
- Tech Scout
- Unparalleled Data Quality
- Higher Quality Content
- 60% Fewer Hallucinations
Browse by: Latest US Patents, China's latest patents, Technical Efficacy Thesaurus, Application Domain, Technology Topic, Popular Technical Reports.
© 2025 PatSnap. All rights reserved.Legal|Privacy policy|Modern Slavery Act Transparency Statement|Sitemap|About US| Contact US: help@patsnap.com