Improving method of thickness uniformity of silicon-based epitaxial wafer
A technology of uniform thickness and epitaxial wafers, applied in chemical instruments and methods, from chemical reactive gases, gaseous chemical plating, etc., can solve problems such as uneven thickness distribution of epitaxial wafers, achieve uniformity of film thickness, improve warping The effect of reducing curvature and film thickness variation
- Summary
- Abstract
- Description
- Claims
- Application Information
AI Technical Summary
Problems solved by technology
Method used
Image
Examples
Embodiment 1
[0020] 1. Place the silicon substrate with (111) crystal orientation on a graphite disk and send it into the reaction chamber, and heat it to 1000°C to grow a 1.5μm thick AlN / AlGaN buffer layer;
[0021] 2. Raise the temperature to 1050° C., and grow a 1 μm thick undoped GaN layer (uGaN).
[0022] 3. A 2 μm thick n-type Si-doped GaN layer is grown on the non-doped GaN layer, that is, an n-type GaN layer. The growth conditions are: pressure 150Torr, temperature 1050°C, graphite disk speed 1200r / min, N 2 、H 2 and NH 3 The flow rates are 64L / min, 120L / min and 50L / min respectively.
[0023] figure 2 Shown is the outer ring of the graphite disc ( figure 1 A schematic diagram of the thickness of the n-type GaN layer grown on a wafer placed in the outer ring of the graphite disk), wherein, figure 2 (a) is a schematic diagram of the surface thickness of the wafer, figure 2 (b) is the thickness diagram of each point in the direction of the arrow. It can be seen from the figur...
Embodiment 2
[0026] 1. Place the silicon substrate with (111) crystal orientation on a graphite disk and send it into the reaction chamber, and heat it to 1000°C to grow a 1.5um thick AlN / AlGaN buffer layer;
[0027] 2. Raise the temperature to 1050°C and grow a 1μm undoped GaN layer (uGaN);
[0028] 3. A 2 μm n-type Si-doped GaN layer is grown on the non-doped GaN layer, that is, an n-type GaN layer. The growth conditions are: pressure 150Torr, temperature 1050°C, graphite rotation speed 500r / min, N 2 、H 2 and NH 3 The flow rates are 10L / min, 70L / min and 45L / min respectively.
[0029] Figure 4 Shown is the outer ring of the graphite disc ( figure 1 A schematic diagram of the thickness of the n-type GaN layer grown on a wafer placed in the outer ring of the graphite disk), wherein, Figure 4 (a) is a schematic diagram of the surface thickness of the wafer, Figure 4 (b) is the thickness map of each point in the direction of the arrow. It can be seen from the figure that along the d...
PUM
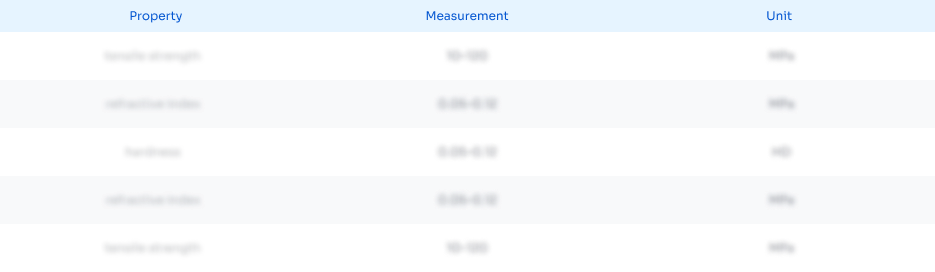
Abstract
Description
Claims
Application Information

- R&D
- Intellectual Property
- Life Sciences
- Materials
- Tech Scout
- Unparalleled Data Quality
- Higher Quality Content
- 60% Fewer Hallucinations
Browse by: Latest US Patents, China's latest patents, Technical Efficacy Thesaurus, Application Domain, Technology Topic, Popular Technical Reports.
© 2025 PatSnap. All rights reserved.Legal|Privacy policy|Modern Slavery Act Transparency Statement|Sitemap|About US| Contact US: help@patsnap.com