Glazing cement and preparation technology thereof
A cement and glazing technology, which is applied in the field of glazing cement preparation technology, can solve the problems of not being able to adapt to energy conservation and emission reduction policies, increase cement production costs, and intensify the mining of mineral resources, and achieve energy saving, low cost, and efficient preparation methods simple effect
- Summary
- Abstract
- Description
- Claims
- Application Information
AI Technical Summary
Problems solved by technology
Method used
Examples
Embodiment 1
[0021] The invention provides a glazed cement, the components of which are calculated in parts by weight: 20 parts of inorganic gel, 2 parts of reinforcing fiber, 4 parts of calcium oxide, 3 parts of magnesium oxide, 3 parts of potassium oxide, basic copper carbonate 1 part, 8 parts of organic modified resin, 2 parts of calcium carbonate, 5 parts of modified tourmaline powder, 8 parts of epoxy resin, 10 parts of iron ore powder, 20 parts of clay, 20 parts of fluorogypsum, 30 parts of river sand, cement reinforcement 10 parts of additive, 0.5 part of retarder, 1 part of modifier, 2 parts of coupling agent, 1 part of regulator, 0.5 part of water reducer, and 0.5 part of toughening agent.
[0022] The present invention also provides a preparation process of glazed cement, comprising the steps of:
[0023] S1. Mix inorganic gel, reinforcing fiber, calcium oxide, magnesium oxide, potassium oxide, basic copper carbonate, organic modified resin, calcium carbonate, and modified tourma...
Embodiment 2
[0028] The invention provides an enamel cement, the components of which are calculated in parts by weight: 25 parts of inorganic gel, 4 parts of reinforcing fiber, 5 parts of calcium oxide, 4 parts of magnesium oxide, 4 parts of potassium oxide, and 2 parts of basic copper carbonate 9 parts of organic modified resin, 3 parts of calcium carbonate, 6 parts of modified tourmaline powder, 9 parts of epoxy resin, 13 parts of iron ore powder, 25 parts of clay, 25 parts of fluorogypsum, 35 parts of river sand, cement reinforcing agent 11 parts, 1 part retarder, 2 parts modifier, 3 parts coupling agent, 2 parts regulator, 1 part water reducer, 1 part toughening agent.
[0029] The present invention also provides a preparation process of enamel cement, comprising the steps of:
[0030] S1. Mix inorganic gel, reinforcing fiber, calcium oxide, magnesium oxide, potassium oxide, basic copper carbonate, organic modified resin, calcium carbonate, and modified tourmaline powder to obtain mixe...
Embodiment 3
[0035] The invention provides an enamel cement, the components of which are calculated in parts by weight: 30 parts of inorganic gel, 6 parts of reinforcing fiber, 6 parts of calcium oxide, 5 parts of magnesium oxide, 5 parts of potassium oxide, and 3 parts of basic copper carbonate 10 parts of organic modified resin, 4 parts of calcium carbonate, 7 parts of modified tourmaline powder, 10 parts of epoxy resin, 15 parts of iron ore powder, 30 parts of clay, 30 parts of fluorogypsum, 40 parts of river sand, cement reinforcing agent 12 parts, 1.5 parts of retarder, 3 parts of modifier, 4 parts of coupling agent, 3 parts of regulator, 1.5 parts of water reducing agent, and 1.5 parts of toughening agent.
[0036] The present invention also provides a preparation process of enamel cement, comprising the steps of:
[0037]S1. Mix inorganic gel, reinforcing fiber, calcium oxide, magnesium oxide, potassium oxide, basic copper carbonate, organic modified resin, calcium carbonate, and mo...
PUM
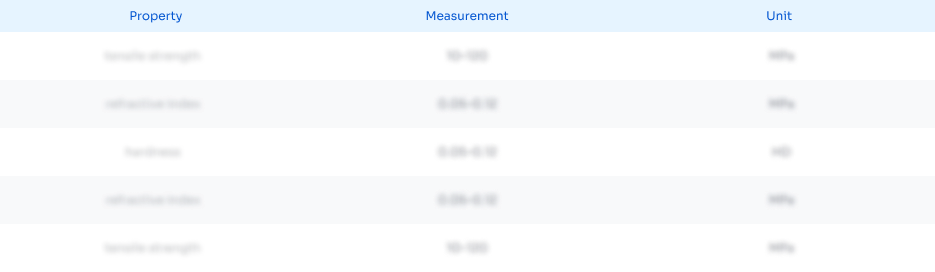
Abstract
Description
Claims
Application Information

- R&D Engineer
- R&D Manager
- IP Professional
- Industry Leading Data Capabilities
- Powerful AI technology
- Patent DNA Extraction
Browse by: Latest US Patents, China's latest patents, Technical Efficacy Thesaurus, Application Domain, Technology Topic, Popular Technical Reports.
© 2024 PatSnap. All rights reserved.Legal|Privacy policy|Modern Slavery Act Transparency Statement|Sitemap|About US| Contact US: help@patsnap.com