Cold heading process for connecting flange of automobile exhaust pipe
A technology for automobile exhaust and connecting flanges, which is applied in the direction of manufacturing tools, metal processing equipment, forging/pressing/hammer devices, etc., can solve the problems of high loss of machining tools, high manufacturing costs, and high material costs, and achieve improved The effect of installing dimensional accuracy, shortening processing time, and optimizing production process
- Summary
- Abstract
- Description
- Claims
- Application Information
AI Technical Summary
Problems solved by technology
Method used
Image
Examples
Embodiment 1
[0039] Such as Figure 1-8 As shown, a cold heading process for connecting flanges of automobile exhaust pipes mainly includes the following steps:
[0040] S1: Making the original bar through a cutting die to obtain a cylindrical blank 1;
[0041] S2: Cold heading the cylindrical blank 1 into a conical shape through the first cold heading die, leaving a machining allowance of 0.5-1 mm to obtain the first semi-finished blank 2;
[0042] S3: cold heading the first semi-finished blank 2 into a rounded truncated shape through the second cold heading die, and extruding the upper end out of the preformed flange 10 to obtain the second semi-finished blank 3;
[0043] S4: Extrude chamfering at both ends of the second semi-finished blank 3 through the third cold heading die, and extrude the upper positioning groove 8 and the lower positioning groove 9 at the upper and lower ends thereof, so as to obtain the third semi-finished blank 4;
[0044] S5: extruding the lower positioning gr...
Embodiment 2
[0050] Such as Figure 1-8 As shown, a cold heading process for connecting flanges of automobile exhaust pipes mainly includes the following steps:
[0051] S1: Making the original bar through a cutting die to obtain a cylindrical blank 1;
[0052] S2: Cold heading the cylindrical blank 1 into a conical shape through the first cold heading die, leaving a machining allowance of 0.5-1 mm to obtain the first semi-finished blank 2;
[0053] S3: cold heading the first semi-finished blank 2 into a rounded truncated shape through the second cold heading die, and extruding the upper end out of the preformed flange 10 to obtain the second semi-finished blank 3;
[0054] S4: Extrude chamfering at both ends of the second semi-finished blank 3 through the third cold heading die, and extrude the upper positioning groove 8 and the lower positioning groove 9 at the upper and lower ends thereof, so as to obtain the third semi-finished blank 4;
[0055] S5: extruding the lower positioning gr...
Embodiment 3
[0061] Such as Figure 1-8 As shown, a cold heading process for connecting flanges of automobile exhaust pipes mainly includes the following steps:
[0062] S1: Making the original bar through a cutting die to obtain a cylindrical blank 1;
[0063] S2: Cold heading the cylindrical blank 1 into a conical shape through the first cold heading die, leaving a machining allowance of 0.5-1 mm to obtain the first semi-finished blank 2;
[0064] S3: cold heading the first semi-finished blank 2 into a rounded truncated shape through the second cold heading die, and extruding the upper end out of the preformed flange 10 to obtain the second semi-finished blank 3;
[0065] S4: Extrude chamfering at both ends of the second semi-finished blank 3 through the third cold heading die, and extrude the upper positioning groove 8 and the lower positioning groove 9 at the upper and lower ends thereof, so as to obtain the third semi-finished blank 4;
[0066] S5: extruding the lower positioning gr...
PUM
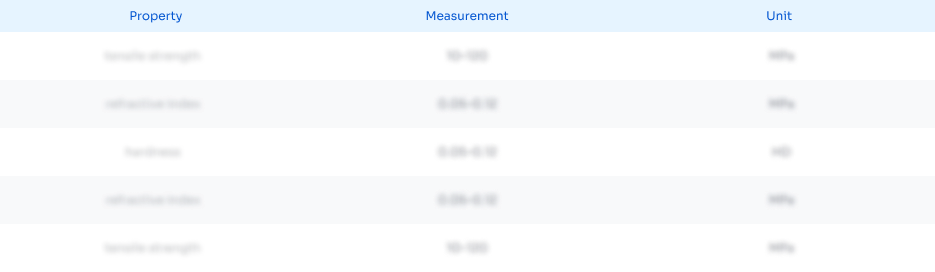
Abstract
Description
Claims
Application Information

- Generate Ideas
- Intellectual Property
- Life Sciences
- Materials
- Tech Scout
- Unparalleled Data Quality
- Higher Quality Content
- 60% Fewer Hallucinations
Browse by: Latest US Patents, China's latest patents, Technical Efficacy Thesaurus, Application Domain, Technology Topic, Popular Technical Reports.
© 2025 PatSnap. All rights reserved.Legal|Privacy policy|Modern Slavery Act Transparency Statement|Sitemap|About US| Contact US: help@patsnap.com