A blade high-rigidity design method based on random isogeometric analysis
An isogeometric analysis and design method technology, applied in the field of ocean current energy power generation, can solve the problems that affect the accurate collection of random response information of blades, affect the accuracy of experimental results, and be unfeasible, achieve high stiffness design, and eliminate approximation errors. , Improve the effect of blade stiffness
- Summary
- Abstract
- Description
- Claims
- Application Information
AI Technical Summary
Problems solved by technology
Method used
Image
Examples
Embodiment Construction
[0047] The present invention will be further described below in conjunction with the accompanying drawings and specific embodiments.
[0048] figure 1 The flow chart is designed for the high stiffness of the blade, and the figure shows the flow chart of the stochastic isogeometric analysis method of the blade. The high stiffness design method of the blade is as follows:
[0049] 1) Airfoil parameterization, the initial airfoil of the blade, design variables and their value ranges are determined according to the airfoil design rules.
[0050] The NACA65421 airfoil was selected as the initial airfoil, which showed excellent hydrodynamic performance in the actual sea test. The airfoil curve of NACA 65421 is divided into four end-to-end curves, and the starting and ending points of the four curves are shown in Table 1.
[0051] Table 1
[0052] curve
starting point
end
1
suction surface apex
2
suction surface apex
lead...
PUM
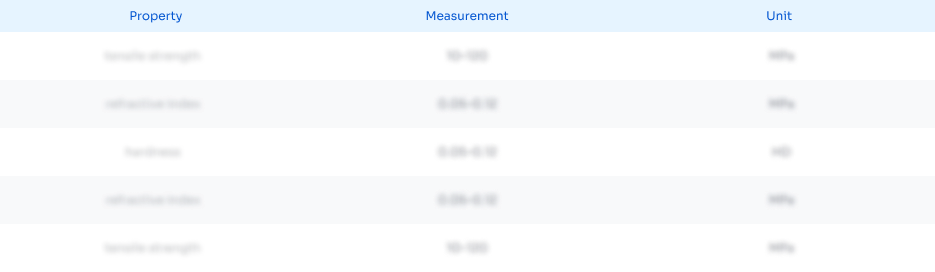
Abstract
Description
Claims
Application Information

- R&D
- Intellectual Property
- Life Sciences
- Materials
- Tech Scout
- Unparalleled Data Quality
- Higher Quality Content
- 60% Fewer Hallucinations
Browse by: Latest US Patents, China's latest patents, Technical Efficacy Thesaurus, Application Domain, Technology Topic, Popular Technical Reports.
© 2025 PatSnap. All rights reserved.Legal|Privacy policy|Modern Slavery Act Transparency Statement|Sitemap|About US| Contact US: help@patsnap.com