A method for calculating fatigue strength of a wind turbine cabin structure
A fatigue strength and calculation method technology, applied in calculation, special data processing applications, instruments, etc., can solve the problems of incomplete consideration of factors, inaccurate calculation of fatigue damage, etc., and achieve the effect of improving safety and reliability
- Summary
- Abstract
- Description
- Claims
- Application Information
AI Technical Summary
Problems solved by technology
Method used
Image
Examples
Embodiment Construction
[0030] The present invention will be further described below in conjunction with the accompanying drawings and embodiments.
[0031] A method for calculating the fatigue strength of a wind turbine nacelle structure, comprising the steps of:
[0032] Step 1: Determination of Stress Spectrum
[0033] Linear fatigue refers to the fatigue caused by the time series of loads under the condition that the component stress varies linearly with the external load. The structural fatigue of the wind turbine nacelle belongs to this type of fatigue. The first is to obtain the linear relationship between the load and the component stress. Generally, the finite element analysis method is used for calculation, that is, the stress time history is calculated by using the linear product of the structural unit load and the finite element calculation result under the gravity load of the generator and the time load history. The stress formula of the wind turbine nacelle structure is as follows (th...
PUM
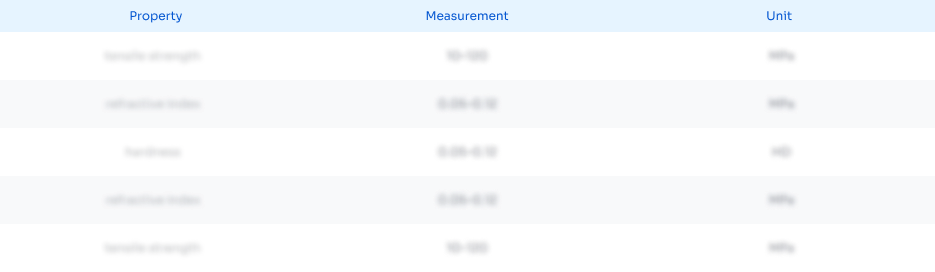
Abstract
Description
Claims
Application Information

- Generate Ideas
- Intellectual Property
- Life Sciences
- Materials
- Tech Scout
- Unparalleled Data Quality
- Higher Quality Content
- 60% Fewer Hallucinations
Browse by: Latest US Patents, China's latest patents, Technical Efficacy Thesaurus, Application Domain, Technology Topic, Popular Technical Reports.
© 2025 PatSnap. All rights reserved.Legal|Privacy policy|Modern Slavery Act Transparency Statement|Sitemap|About US| Contact US: help@patsnap.com