Laser-effect coating composition for PP substrate and preparation method thereof
A composition and coating technology, applied in the direction of coating, etc., to achieve the effect of stable storage, moderate price and low cost
- Summary
- Abstract
- Description
- Claims
- Application Information
AI Technical Summary
Problems solved by technology
Method used
Image
Examples
Embodiment 1
[0030] The PP substrate laser effect coating composition of this embodiment is prepared by using the raw materials of the components and contents shown in Table 1; the specific preparation includes the following process steps:
[0031] (1) 30 kilograms of acetone, 20 kilograms of n-propyl acetate and 20 kilograms of n-butyl acetate are all dropped into the reactor, and stirred evenly;
[0032] (2) 1.5 kilograms of urea-formaldehyde resins and 2.5 kilograms of benzomelamine-formaldehyde resins are dropped into the reactor, stirred at high speed for 1.5 hours until fully dissolved;
[0033] (3) Add 6 kg of chlorinated polyethylene resin and 19.5 kg of butanol etherified phenolic resin into the reaction kettle, stir at high speed for 2.5 hours until fully dissolved
[0034] (4) Slowly add 0.2 kg of leveling agent (polydimethylsiloxane), 0.2 kg of slip agent (stearic acid amide), and 0.1 kg of drier (neodecanoic acid) into the reactor in sequence, fully Stir until well dispersed....
Embodiment 2
[0037] The PP substrate laser effect coating composition of this embodiment is prepared by using the raw materials of the components and contents shown in Table 1; the specific preparation includes the following process steps:
[0038] (1) 55 kilograms of ethyl acetate and 20 kilograms of propylene glycol methyl ether are all dropped into the reactor, and stirred evenly;
[0039] (2) 2 kilograms of melamine-formaldehyde resins and 2 kilograms of benzomelamine-formaldehyde resins are dropped into the reactor, and stirred at a high speed for 1.5 hours to fully dissolve;
[0040] (3) Add 8 kilograms of chlorinated polyethylene resin, 3 kilograms of chlorinated polypropylene resin, and 10 kilograms of oil-soluble pure phenolic resin into the reaction kettle, stir at high speed for 2.5 hours, until fully dissolved;
[0041] (4) Slowly add 0.01 kg of flow cross-linking agent (diethylene triamine) into the reaction kettle, stir well until the dispersion is uniform.
[0042] Apply th...
Embodiment 3
[0044] The PP substrate laser effect coating composition of this embodiment is prepared by using the raw materials of the components and contents shown in Table 1; the specific preparation includes the following process steps:
[0045] (1) 33 kilograms of isopropanols, 20 kilograms of n-butanols and 20 kilograms of propylene glycol methyl ether acetate are all dropped into the reactor, and stirred;
[0046] (2) 0.5 kg of urea-formaldehyde resin, 0.5 kg of melamine-formaldehyde resin, and 0.5 kg of benzomelamine-formaldehyde resin are dropped into the reactor, and stirred at a high speed for 2.0 hours to fully dissolve;
[0047] (3) 7 kilograms of chlorinated polyethylene resins, 2 kilograms of chlorinated ethylene-propylene copolymer resins, and 13.7 kilograms of butanol etherified phenolic resins are added in the reactor, stirred at high speed for 2.5 hours, until fully dissolved;
[0048] (4) Slowly add 0.2 kg of leveling agent (polydimethylsiloxane) and 0.1 kg of slip agent...
PUM
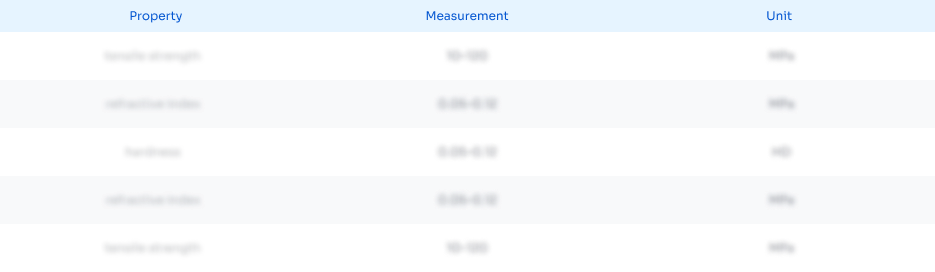
Abstract
Description
Claims
Application Information

- R&D
- Intellectual Property
- Life Sciences
- Materials
- Tech Scout
- Unparalleled Data Quality
- Higher Quality Content
- 60% Fewer Hallucinations
Browse by: Latest US Patents, China's latest patents, Technical Efficacy Thesaurus, Application Domain, Technology Topic, Popular Technical Reports.
© 2025 PatSnap. All rights reserved.Legal|Privacy policy|Modern Slavery Act Transparency Statement|Sitemap|About US| Contact US: help@patsnap.com