Double-side high-smoothness pulp molding product shaping system and shaping method
A technology of pulp molding and forming methods, which is applied in the direction of textiles and papermaking, can solve the problems of long process time and achieve the effect of improving production cycle and production cycle
- Summary
- Abstract
- Description
- Claims
- Application Information
AI Technical Summary
Problems solved by technology
Method used
Image
Examples
Embodiment 1
[0044] A double-sided high-smoothness pulp molding product forming system provided in this embodiment, see figure 1 As shown, according to the sequence of preparation of pulp molded products, it includes: suction mold 2 forms a wet embryo after sucking pulp from the pulp tank 1; After the embryo is reversed upwards, the wet embryo is extruded with the extrusion die 3 for the first time; the hot pressing upper die 4 can move up and down in the vertical direction; the hot pressing lower die 5 can move left and right in the horizontal direction. When the lower mold 5 corresponds up and down, the wet embryo is hot-pressed; the hot-pressing upper mold 4 is provided with an air suction structure, and the hot-pressing lower mold 5 is provided with an air-blowing structure; the hot-pressing lower mold 5 and placed under the hot-pressing The new transfer mold 8 on the downstream side of the mold 5 is fixed on the horizontal slide plate, and the formed molded product in the new transfer...
Embodiment 2
[0051] This embodiment provides a molding method of pulp molding, see Figure 9 shown, including the following steps:
[0052] After the pulp suction die 2 sucks the pulp from the pulp tank 1, it turns over, squeezes with the extrusion die 3 on it, and turns over again after extrusion. At this time, the hot pressing lower die 5 moves to the left to the pulp suction die 2 Below, the slurry suction mold 2 places the wet embryo in the hot-pressing lower mold 5. At this time, the station 1 is formed, and the hot-pressing lower mold 5 moves to the right to the position corresponding to the hot-pressing upper mold 4 to form a station 2. At this time, the hot-pressing upper die 4 moves vertically downward, squeezes the wet embryo with the hot-pressing lower die 5 and heats it to shape. There is a blowing structure, therefore, the molded product formed here is on the hot-pressing upper mold 4, and then the hot-pressing lower mold 5 and the unloading clamp move to the left together, a...
Embodiment 3
[0057] This embodiment provides a method for forming a double-sided high-smooth pulp molded product, comprising the following steps,
[0058] S1. Adsorb the slurry on the surface of the corresponding upper and lower slurry suction molds to obtain the original double-layer blank;
[0059] S2. The hot-pressing lower die moves to the left, and the above-mentioned wet blanks of the positive cavity and the wet blanks of the negative cavity are placed in the lower hot-pressing die according to the rough surface, and the upper hot-pressing die moves downward to extrude and heat. The temperature is 80°C, heating for 5 minutes; at the same time, after the heating is completed, the hot-pressing upper mold and the hot-pressing lower mold are separated, and the molded products are absorbed and transferred by the hot-pressing upper mold;
[0060] S3. The hot-pressing lower mold and the unloading fixture move to the left together, and return to station 1. At this time, the hot-pressing uppe...
PUM
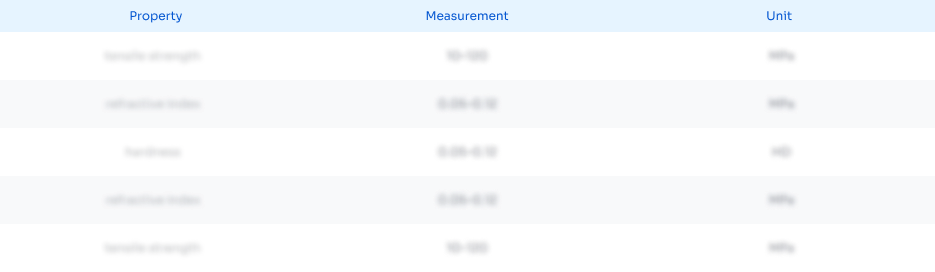
Abstract
Description
Claims
Application Information

- Generate Ideas
- Intellectual Property
- Life Sciences
- Materials
- Tech Scout
- Unparalleled Data Quality
- Higher Quality Content
- 60% Fewer Hallucinations
Browse by: Latest US Patents, China's latest patents, Technical Efficacy Thesaurus, Application Domain, Technology Topic, Popular Technical Reports.
© 2025 PatSnap. All rights reserved.Legal|Privacy policy|Modern Slavery Act Transparency Statement|Sitemap|About US| Contact US: help@patsnap.com