A kind of polishing method of large polishing machine
A polishing machine and polishing wheel technology, which is applied to surface polishing machine tools, grinding machine parts, and grinding/polishing equipment, etc., can solve the problems of limited operation speed, large labor cost, and inability to meet automatic polishing applications. Achieve the effect of satisfying real-time adjustment and ensuring constant force
- Summary
- Abstract
- Description
- Claims
- Application Information
AI Technical Summary
Problems solved by technology
Method used
Image
Examples
Embodiment Construction
[0032] In order to enable those skilled in the art to better understand the technical solution of the present invention, its specific implementation will be described in detail below in conjunction with the accompanying drawings:
[0033] see figure 1 , figure 2 and image 3 , the most preferred embodiment of the present invention, a kind of polishing method of large polishing machine, following steps:
[0034] S1, the steps of designing a large polishing machine: the large polishing machine includes a casing 1, an electric control cabinet 2, a first DC brushless motor 3, a second DC brushless motor 4, a force control mechanism, a polishing wheel bracket 6, and a timing belt 7. Polishing wheel assembly shaft 8, polishing wheel 9 and wax spraying mechanism.
[0035] The electric control cabinet 2 is arranged on the outside of the left side wall of the casing 1; the first DC brushless motor 3 and the second DC brushless motor 4 are arranged on the left side wall of the casin...
PUM
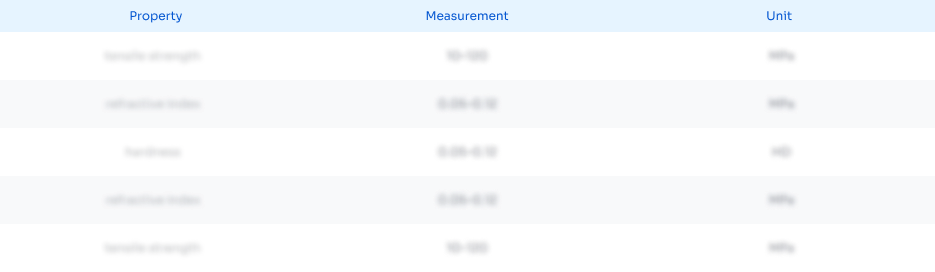
Abstract
Description
Claims
Application Information

- R&D Engineer
- R&D Manager
- IP Professional
- Industry Leading Data Capabilities
- Powerful AI technology
- Patent DNA Extraction
Browse by: Latest US Patents, China's latest patents, Technical Efficacy Thesaurus, Application Domain, Technology Topic, Popular Technical Reports.
© 2024 PatSnap. All rights reserved.Legal|Privacy policy|Modern Slavery Act Transparency Statement|Sitemap|About US| Contact US: help@patsnap.com