Catalyst system for preparing hydrocarbons and use thereof
A catalyst, a technology for producing hydrocarbons, applied in molecular sieve catalysts, chemical instruments and methods, catalyst activation/preparation, etc., can solve the problems of inconvenient filling, low selectivity of target products aromatics, low CO conversion rate, etc.
- Summary
- Abstract
- Description
- Claims
- Application Information
AI Technical Summary
Problems solved by technology
Method used
Image
Examples
Embodiment 1
[0052] Preparation of Manganese Oxide Mn by Precipitation Method 2 o 3 , the HZSM-5 molecular sieve with a Si / Al ratio of 12 was synthesized by a hydrothermal method, and the obtained molecular sieve was denoted as HZ5(12); the Mn 2 o 3 , HZ5(12) powder is mechanically mixed according to the mass ratio of 1:1, then granulated and crushed to obtain catalyst particles of 20-40 mesh. Weigh 1.5g of catalyst particles and load them into the reactor. At a reaction temperature of 395°C and a pressure of 2.0MPa, the feed gas H 2 / CO ratio 1.0, airspeed 2000h -1 Catalyst evaluation was carried out under the conditions. Before the reaction, the catalyst was heated with H at 395°C 2 Pretreatment 2h.
[0053] Feed gas H 2 / CO / N 2 , the product was analyzed online by gas chromatography, where N 2 Quantitative analysis of the product was achieved for the internal standard. The product is separated by three columns, one of which is a hayesep-Q packed column, and the separated prod...
Embodiment 2
[0055] Preparation of Chromium Oxide Cr by Precipitation Method 2 o 3 , the HZSM-5 molecular sieve with a Si / Al ratio of 12 was synthesized by a hydrothermal method, and the obtained molecular sieve was denoted as HZ5(12); the Cr 2 o 3 , HZ5(12) powder is mechanically mixed according to the mass ratio of 1:1, then granulated and crushed to obtain catalyst particles of 20-40 mesh. Weigh 1.5g of catalyst particles and load them into the reactor. At a reaction temperature of 395°C and a pressure of 2.0MPa, the feed gas H 2 / CO ratio 1.0, airspeed 2000h -1 Catalyst evaluation was carried out under the conditions. Before the reaction, the catalyst was heated with H at 395°C 2 Pretreatment 2h. The results of CO conversion and product selectivity are shown in Table 1.
Embodiment 3
[0057] Preparation of Cerium Oxide CeO by Hydrothermal Method 2 , the HZSM-5 molecular sieve with a Si / Al ratio of 12 was synthesized by a hydrothermal method, and the obtained molecular sieve was denoted as HZ5(12); the CeO 2 , HZ5(12) powder is mechanically mixed according to the mass ratio of 1:1, then granulated and crushed to obtain catalyst particles of 20-40 mesh. Weigh 1.5g of catalyst particles and load them into the reactor. At a reaction temperature of 395°C and a pressure of 2.0MPa, the feed gas H 2 / CO ratio 1.0, airspeed 2000h -1 Catalyst evaluation was carried out under the conditions. Before the reaction, the catalyst was heated with H at 395°C 2 Pretreatment 2h. The results of CO conversion and product selectivity are shown in Table 1.
PUM
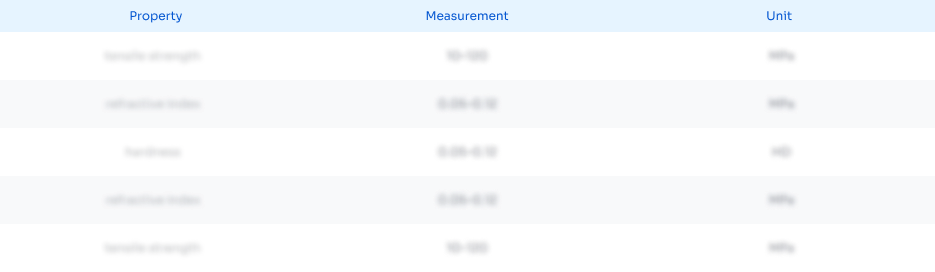
Abstract
Description
Claims
Application Information

- R&D Engineer
- R&D Manager
- IP Professional
- Industry Leading Data Capabilities
- Powerful AI technology
- Patent DNA Extraction
Browse by: Latest US Patents, China's latest patents, Technical Efficacy Thesaurus, Application Domain, Technology Topic, Popular Technical Reports.
© 2024 PatSnap. All rights reserved.Legal|Privacy policy|Modern Slavery Act Transparency Statement|Sitemap|About US| Contact US: help@patsnap.com