System and method for detecting and stabilizing effective anchorage prestressing force tested by clip piece displacement method
A technology of prestress and displacement method, used in measuring devices, force/torque/work measuring instruments, instruments, etc., can solve the problems of large test results, small friction resistance of clips, small test results, etc., and achieve high detection reliability. , The effect of stable force value output and less detection problems
- Summary
- Abstract
- Description
- Claims
- Application Information
AI Technical Summary
Problems solved by technology
Method used
Image
Examples
Embodiment 1
[0033] Such as figure 2 As shown, a system for detecting and stabilizing clip displacement method to detect the effective prestress under the anchor, including the main control terminal 12, the detection terminal 11, the self-locking electromagnetic reversing control hydraulic system, the bridge pressure sensor 9 and the displacement measurement Tooling 6;
[0034] The main control terminal 12 is connected with the detection terminal 11 through wireless WIFI, the main control terminal 12 is connected with the self-locking electromagnetic reversing control hydraulic system signal, and the detection terminal 11 is connected with the bridge pressure sensor 9 and the displacement measurement tooling respectively. 6 signal connections;
[0035]The self-locking electromagnetic reversing control hydraulic system includes an actuator 10-1, an oil pump 10-2, and an oil pipe 10-3 connecting the actuator 10-1 and the oil pump 10-2, and the oil pipe 10-3 is an ultra-high pressure resin ...
Embodiment 2
[0046] A detection method using the detection and stabilization clip displacement method described in embodiment 1 to detect the effective prestress under the anchor system, comprising the steps:
[0047] S1. Install the detection system, pass the steel strand through the anchor head, clip, tool anchor of the displacement measurement tool, bridge pressure sensor, and then connect it to the actuator of the self-locking electromagnetic reversing control hydraulic system, and the steel strand The wire is also fixedly connected with the clip, so that the anchor head, the clip, the displacement transmission mechanism, and the Hall displacement sensor are in close contact, and the displacement measurement tool, the bridge pressure sensor and the self-locking electromagnetic reversing control hydraulic system are in close contact;
[0048] S2. The detection system is pre-tightened, and the Hall displacement sensor, the bridge pressure sensor, the self-locking electromagnetic reversing...
PUM
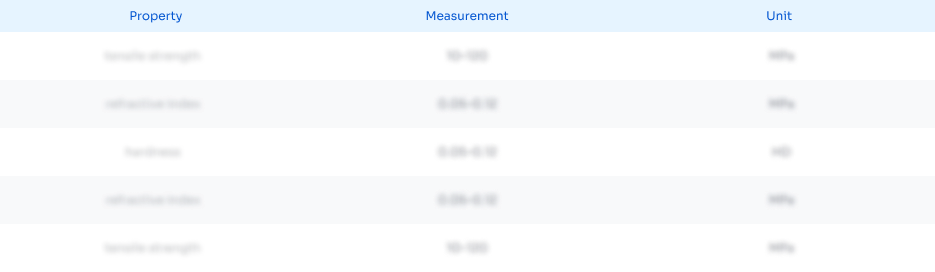
Abstract
Description
Claims
Application Information

- R&D Engineer
- R&D Manager
- IP Professional
- Industry Leading Data Capabilities
- Powerful AI technology
- Patent DNA Extraction
Browse by: Latest US Patents, China's latest patents, Technical Efficacy Thesaurus, Application Domain, Technology Topic, Popular Technical Reports.
© 2024 PatSnap. All rights reserved.Legal|Privacy policy|Modern Slavery Act Transparency Statement|Sitemap|About US| Contact US: help@patsnap.com