Light composite thermal insulation wallboard and preparation method thereof
A composite thermal insulation and wall panel technology, applied in building components, building materials, buildings, etc., can solve problems such as poor mechanical properties and poor thermal insulation, and achieve the effect of strong hanging force, easy implementation, and low equipment requirements.
- Summary
- Abstract
- Description
- Claims
- Application Information
AI Technical Summary
Problems solved by technology
Method used
Image
Examples
Embodiment 1
[0026] A lightweight composite thermal insulation wallboard, comprising an upper panel layer and a lower panel layer, a filling layer is arranged between the upper panel layer and the lower panel layer; in parts by weight, the filling layer is mainly made of the following raw materials: Ingredients: 110 parts of cement, 50 parts of polystyrene particles, 11 parts of hydroquinone, 7 parts of maleic anhydride, 10 parts of zeolite powder, 6 parts of vinyl phosphate, 16 parts of redispersible latex; 25 parts of desulfurized gypsum powder, 23 parts of glass fiber, 13 parts of water reducing agent, 32 parts of mineral powder, 11 parts of potassium aluminum sulfate dodecahydrate, 14 parts of sodium hexametaphosphate, 23 parts of diatomaceous earth, 11 parts of lignin, 13 parts of silane coupling agent, 13 parts of formamide, 18 parts of sodium metaaluminate, 19 parts of kaolin, 13 parts of simethicone, 13 parts of aluminum sulfate and 19 parts of ceramsite.
[0027] The water reducer...
Embodiment 2
[0038] A lightweight composite thermal insulation wallboard, comprising an upper panel layer and a lower panel layer, a filling layer is arranged between the upper panel layer and the lower panel layer; in parts by weight, the filling layer is mainly made of the following raw materials: Ingredients: 80 parts of cement, 60 parts of polystyrene particles, 7 parts of hydroquinone, 11 parts of maleic anhydride, 13 parts of zeolite powder, 3 parts of vinyl phosphate, 25 parts of redispersible latex; 10 parts of desulfurized gypsum powder, 15 parts of glass fiber, 5 parts of water reducing agent, 40 parts of mineral powder, 16 parts of potassium aluminum sulfate dodecahydrate, 8 parts of sodium hexametaphosphate, 16 parts of diatomaceous earth, 19 parts of lignin, 7 parts of silane coupling agent, 19 parts of formamide, 11 parts of sodium metaaluminate, 15 parts of kaolin, 3 parts of simethicone, 17 parts of aluminum sulfate and 28 parts of ceramsite.
[0039] The water reducer is s...
Embodiment 3
[0050] A lightweight composite thermal insulation wallboard, comprising an upper panel layer and a lower panel layer, a filling layer is arranged between the upper panel layer and the lower panel layer; in parts by weight, the filling layer is mainly made of the following raw materials: Ingredients: 140 parts of cement, 35 parts of polystyrene particles, 14 parts of hydroquinone, 4 parts of maleic anhydride, 8 parts of zeolite powder, 9 parts of vinyl phosphate, 10 parts of redispersible latex; 35 parts of desulfurized gypsum powder, 35 parts of glass fiber, 18 parts of water reducing agent, 25 parts of mineral powder, 3 parts of potassium aluminum sulfate dodecahydrate, 22 parts of sodium hexametaphosphate, 28 parts of diatomaceous earth, 8 parts of lignin, 17 parts of silane coupling agent, 6 parts of formamide, 25 parts of sodium metaaluminate, 25 parts of kaolin, 18 parts of simethicone, 4 parts of aluminum sulfate and 12 parts of ceramsite.
[0051] The water reducer is Y...
PUM
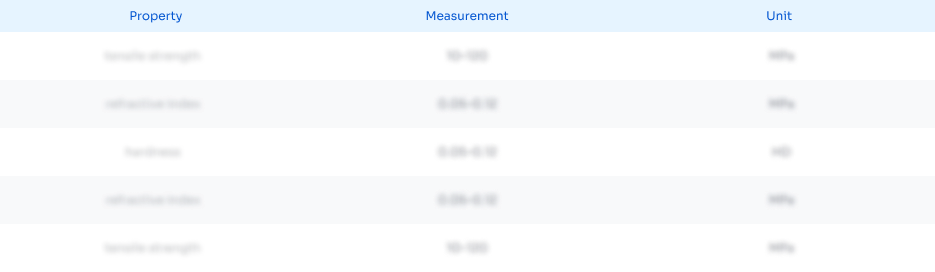
Abstract
Description
Claims
Application Information

- R&D
- Intellectual Property
- Life Sciences
- Materials
- Tech Scout
- Unparalleled Data Quality
- Higher Quality Content
- 60% Fewer Hallucinations
Browse by: Latest US Patents, China's latest patents, Technical Efficacy Thesaurus, Application Domain, Technology Topic, Popular Technical Reports.
© 2025 PatSnap. All rights reserved.Legal|Privacy policy|Modern Slavery Act Transparency Statement|Sitemap|About US| Contact US: help@patsnap.com