Manufacturing process for environment-friendly polymer pen point of skin-core structure
A technology of skin-core structure and manufacturing process, which is applied in the direction of nibs, printing, writing utensils, etc., can solve the problems of affecting writing effect, long water diversion time, disordered arrangement of skin-core composite fiber filaments, etc., to achieve good writing effect and easy to use Labor-saving effect
- Summary
- Abstract
- Description
- Claims
- Application Information
AI Technical Summary
Problems solved by technology
Method used
Image
Examples
Embodiment Construction
[0032] Such as figure 1 — image 3 As shown, the invention discloses a manufacturing process of a skin-core structure environment-friendly polymer nib,
[0033] The first step is to select materials, choose nylon 6 as the cortex fiber 1, and nylon 66 as the core fiber 2;
[0034] In the second step, compounding, the skin layer fiber 1 is attached to the periphery of the core layer fiber 2 by a composite spinning method to form a skin-core composite fiber filament 3, and the thickness 2a of the skin layer fiber 1 and the thickness 2b ratio of the core layer fiber 2 are 15 / 85 —5 / 95;
[0035] The third step is stranding, selecting a number of skin-core composite fiber filaments 3 and stranding to form composite fiber strands 4;
[0036] The fourth step is to vibrate the single-strand composite fiber tow 4 repeatedly at high frequency until each skin-core composite fiber 3 is vibrated to be evenly arranged;
[0037] The fifth step is forming. The composite fiber tow 4 is heate...
PUM
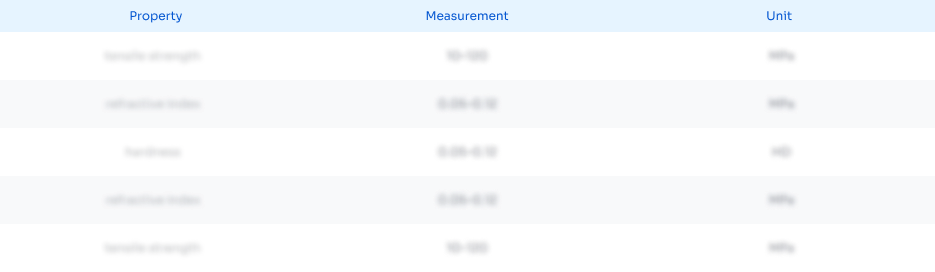
Abstract
Description
Claims
Application Information

- R&D
- Intellectual Property
- Life Sciences
- Materials
- Tech Scout
- Unparalleled Data Quality
- Higher Quality Content
- 60% Fewer Hallucinations
Browse by: Latest US Patents, China's latest patents, Technical Efficacy Thesaurus, Application Domain, Technology Topic, Popular Technical Reports.
© 2025 PatSnap. All rights reserved.Legal|Privacy policy|Modern Slavery Act Transparency Statement|Sitemap|About US| Contact US: help@patsnap.com