Precious metal alloy purification and enrichment technology and oxidizing refining furnace
An oxidation refining, purification and enrichment technology, applied in the direction of improving process efficiency, can solve the problems of high production cost, low recovery rate of lead oxide, low direct recovery rate of gold and silver, etc., to achieve significant production benefits, direct recovery High efficiency and good separation effect
- Summary
- Abstract
- Description
- Claims
- Application Information
AI Technical Summary
Problems solved by technology
Method used
Image
Examples
Embodiment Construction
[0037] The present invention will be further described below in conjunction with the examples, but the present invention is not limited in any way, and any transformation made based on the teaching of the present invention falls within the protection scope of the present invention.
[0038] Reference attached figure 2 A precious metal alloy purification and enrichment process, including reduction smelting of anode slime containing lead, bismuth and tin, separation of gold and silver alloys in a vacuum furnace, and removal of impurities in an oxidation refining furnace to obtain gold and silver alloys with higher purity, so that gold and silver can be directly The yield is increased to 97.5-99%; in the oxidation refining process, the lead oxide volatilized as gas accounts for 1.5% of the total lead oxide weight; 98.5% of the lead oxide is infiltrated and absorbed by the porous hearth (8) cylinder body .
[0039] An oxidation refining furnace for purifying and enriching gold a...
PUM
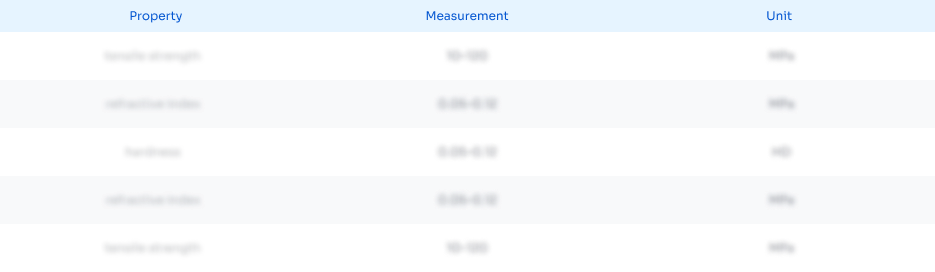
Abstract
Description
Claims
Application Information

- R&D Engineer
- R&D Manager
- IP Professional
- Industry Leading Data Capabilities
- Powerful AI technology
- Patent DNA Extraction
Browse by: Latest US Patents, China's latest patents, Technical Efficacy Thesaurus, Application Domain, Technology Topic, Popular Technical Reports.
© 2024 PatSnap. All rights reserved.Legal|Privacy policy|Modern Slavery Act Transparency Statement|Sitemap|About US| Contact US: help@patsnap.com