Preparing method and product of hydrophobic sulfur-resistant low-temperature denitration catalyst
A low-temperature denitrification and catalyst technology, which is applied in the field of denitrification catalysts, can solve the problem that the denitrification catalysts of power plants cannot meet the requirements of industrial kiln (boiler) furnace denitrification purification, the decomposition temperature of ammonium sulfate or ammonium bisulfate is not reached, ammonium sulfate or ammonium bisulfate Poisoning inactivation and other problems, to achieve the effect of slowing down the rate of poisoning inactivation, low equipment requirements, and reducing deposition
- Summary
- Abstract
- Description
- Claims
- Application Information
AI Technical Summary
Problems solved by technology
Method used
Image
Examples
Embodiment 1
[0027] Preparation of hydrophobic sulfur-resistant low-temperature denitrification catalyst
[0028] (1) Preparation of TiO 2 -SiO 2 Composite carrier
[0029] Add 15L of tetra-n-butyl titanate into a mixture of 4.5L of acetylacetone and 8.82L of absolute ethanol, and stir for 4 hours to obtain solution A;
[0030] Add 2.43L tetraethyl orthosilicate, 26.40g lauryl ammonium sulfate, 66g P127, 65L ethanol and 26.88L ammonia water into 11.65L water, and stir for 4 hours to obtain solution B;
[0031] Add solution B into solution A, mix well to obtain colloid, place the colloid for 2 days, calcinate at 450°C for 4 hours, and cool to room temperature to obtain TiO 2 -SiO 2 Composite carrier, TiO in the composite carrier 2 and SiO 2 The mass ratio is 5:1;
[0032] (2) Preparation of precursor solution
[0033] Add 0.23L of monoethanolammonium, 0.26kg of ammonium metavanadate and 0.61kg of ammonium heptamolybdate into water at 80°C, mix well to prepare the precursor solution;...
Embodiment 2
[0037] Preparation of hydrophobic sulfur-resistant low-temperature denitrification catalyst
[0038] (1) Preparation of TiO 2 -SiO 2 Composite carrier
[0039] Add 14.4L of tetra-n-butyl titanate into a mixture of 4.32L of acetylacetone and 8.47L of absolute ethanol, and stir for 3 hours to obtain solution A;
[0040] Add 2.92L tetraethyl orthosilicate, 32.3g lauryl ammonium sulfate, 78g P127, 25.95L ethanol and 32.2L ammonia water into 14L water, and stir for 3 hours to obtain solution B;
[0041]Add solution B into solution A, mix well to obtain colloid, place the colloid for 1 day, calcinate at 400°C for 5 hours, and cool to room temperature to obtain TiO 2 -SiO 2 Composite carrier, TiO in the composite carrier 2 and SiO 2 The mass ratio is 4:1;
[0042] (2) Preparation of precursor solution
[0043] Add 0.23L of monoethanolammonium, 0.26kg of ammonium metavanadate and 0.61kg of ammonium heptamolybdate into water at 90°C, mix well to prepare the precursor solution; ...
Embodiment 3
[0047] Preparation of hydrophobic sulfur-resistant low-temperature denitrification catalyst
[0048] (1) Preparation of TiO 2 -SiO 2 Composite carrier
[0049] Add 13.5L of tetra-n-butyl titanate into a mixture of 4.05L of acetylacetone and 7.94L of absolute ethanol, and stir for 4 hours to obtain solution A;
[0050] Add 3.65L tetraethyl orthosilicate, 39.63g ammonium lauryl sulfate, 96g P127, 32.44L ethanol and 40.25L ammonia water into 17.50L water, and stir for 4 hours to obtain solution B;
[0051] Add solution B to solution A, mix well to obtain colloid, place the colloid for 3 days, calcinate at 450°C for 4 hours, and cool to room temperature to obtain TiO 2 -SiO 2 Composite carrier, TiO in the composite carrier 2 and SiO 2 The mass ratio is 3:1;
[0052] (2) Preparation of precursor solution
[0053] Add 0.23L of monoethanolammonium, 0.26kg of ammonium metavanadate and 0.61kg of ammonium heptamolybdate into water at 80°C, mix well to prepare the precursor solut...
PUM
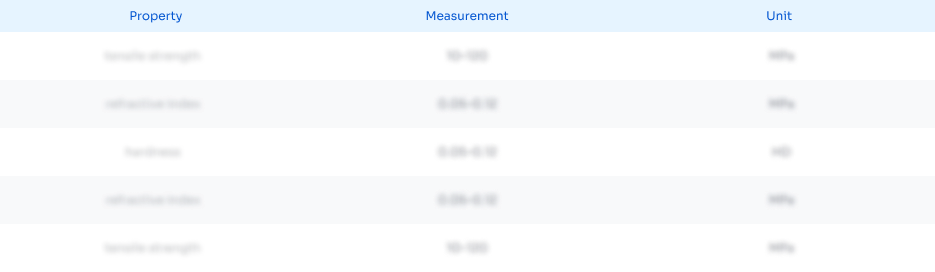
Abstract
Description
Claims
Application Information

- R&D Engineer
- R&D Manager
- IP Professional
- Industry Leading Data Capabilities
- Powerful AI technology
- Patent DNA Extraction
Browse by: Latest US Patents, China's latest patents, Technical Efficacy Thesaurus, Application Domain, Technology Topic, Popular Technical Reports.
© 2024 PatSnap. All rights reserved.Legal|Privacy policy|Modern Slavery Act Transparency Statement|Sitemap|About US| Contact US: help@patsnap.com