A molybdenum-aluminum common etching solution and an etching method
An etchant and molybdenum-aluminum technology, which is applied in the field of molybdenum-aluminum common etchant for low-temperature polysilicon, can solve the problems of high cost and low etching efficiency
- Summary
- Abstract
- Description
- Claims
- Application Information
AI Technical Summary
Problems solved by technology
Method used
Image
Examples
Embodiment 1-3、 comparative example 1-6
[0030] The examples and comparative examples are used to illustrate the molybdenum-aluminum common etching solution and etching method disclosed in the present invention.
[0031] A barrier film made of molybdenum-based materials and a molybdenum / aluminum / molybdenum-based multilayer film made of a material mainly composed of aluminum are sequentially laminated on a glass substrate by sputtering. etched coating pattern.
[0032] The etching temperature of the glass substrate was 35°C. After etching, rinse with pure water and dry. Etching residue, etching uniformity (whether bubbles are produced), Taper Angle, and CD Loss are evaluated by the following standards, and the etching solution formula and etching time of embodiment 1-3 and comparative example 1-6 are as shown in table 1. The test evaluation results are shown in Table 2.
[0033] Table 1
[0034]
[0035] Table 2
[0036]
Embodiment 1
[0037] The SEM results of the LS layer and the M3 layer after the etching of embodiment 1 are respectively as follows figure 1 with figure 2 shown. The SEM results of the LS layer and the M3 layer after the etching of embodiment 3 are respectively as follows image 3 with Figure 4 shown.
[0038] As can be seen from the SEM images of the test results in Table 2 and accompanying drawings, the common etching solution for molybdenum and aluminum provided by the present invention can not only be used to etch the LS layer (molybdenum film), but also can etch the M3 layer (molybdenum aluminum molybdenum film) simultaneously. Fast, good etch quality. At the same time, it can be seen from the test results of Comparative Examples 1-3 and Comparative Examples 3-4 that when the metal salt and ammonium salt content in the etching solution are too high or too low, it is not conducive to the improvement of etching efficiency, and the etching quality is reduced.
PUM
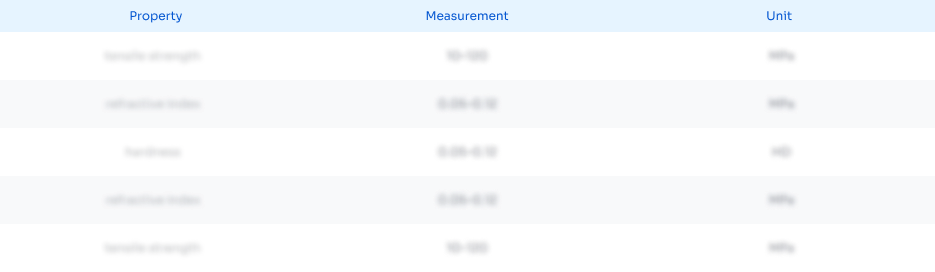
Abstract
Description
Claims
Application Information

- R&D
- Intellectual Property
- Life Sciences
- Materials
- Tech Scout
- Unparalleled Data Quality
- Higher Quality Content
- 60% Fewer Hallucinations
Browse by: Latest US Patents, China's latest patents, Technical Efficacy Thesaurus, Application Domain, Technology Topic, Popular Technical Reports.
© 2025 PatSnap. All rights reserved.Legal|Privacy policy|Modern Slavery Act Transparency Statement|Sitemap|About US| Contact US: help@patsnap.com