Wet parison product extruding and dewatering mold assembly, plant fiber vacuum forming machine with same, and dewatering technique
A technology of extrusion dehydration and blister molding, applied in textiles and papermaking, etc., can solve the problems affecting the overall strength and hardness of products, high labor intensity of operators, uneven surface of mold blanks, etc. The effect of flat appearance and uniform internal density
- Summary
- Abstract
- Description
- Claims
- Application Information
AI Technical Summary
Problems solved by technology
Method used
Image
Examples
Embodiment Construction
[0017] The wet billet product extrusion dewatering mold assembly provided by this patent application, such as figure 1 As shown, its composition includes a mold body 1 and an airtight film 2 . The mold body 1 has a contoured inner mold surface 10 corresponding to the concave-convex mold surface of the blister forming mold assembly B, and the airtight membrane 2 is made of flexible elastic material, such as silica gel, flexible rubber, etc. On the contoured inner mold face 10 of the mold body 1 , its edge fits in an airtight manner with the mold body 1 . In order to attract jade, Figure 4 , 5 An implementation structure of detachable airtight fitting assembly of the airtight membrane 2 and the mold body 1 is given. The structure includes an edge pressing frame 7, the size of the edge pressing frame 7 is consistent with the surrounding edges of the airtight film 2, and a convex-concave matching slot 8 for buckling the airtight film is provided between the edge pressing frame...
PUM
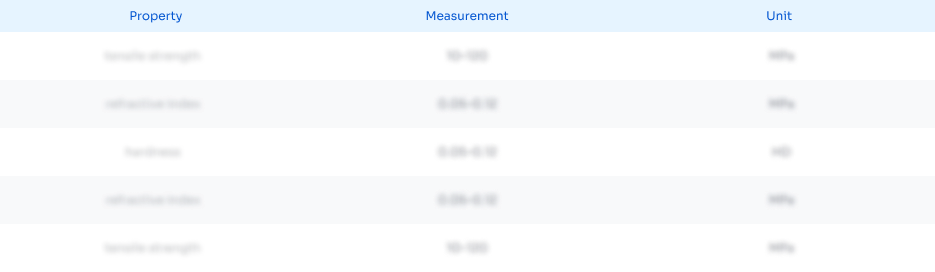
Abstract
Description
Claims
Application Information

- R&D Engineer
- R&D Manager
- IP Professional
- Industry Leading Data Capabilities
- Powerful AI technology
- Patent DNA Extraction
Browse by: Latest US Patents, China's latest patents, Technical Efficacy Thesaurus, Application Domain, Technology Topic, Popular Technical Reports.
© 2024 PatSnap. All rights reserved.Legal|Privacy policy|Modern Slavery Act Transparency Statement|Sitemap|About US| Contact US: help@patsnap.com