Oxide inclusion control method for producing ultra-low-carbon steel by using LD-RH process
A technology of ultra-low carbon steel and control method, which is applied to the improvement of process efficiency and the manufacture of converters, etc. It can solve the problems such as difficult to determine the process effect, achieve remarkable cleaning effect, improve product quality, reduce the number of oxide inclusions and finished products The effect of oxygen content
- Summary
- Abstract
- Description
- Claims
- Application Information
AI Technical Summary
Problems solved by technology
Method used
Image
Examples
Embodiment 1
[0030]Converter blowing is completed, [C]=280ppm, [O]=650ppm, slag is blocked and tapped to ensure ladle slag thickness ≤ 50mm, lime 2.2-2.5kg / t steel is added at the beginning of tapping, and aluminum slag is added at the end of 0.8-1.0kg / t steel, ladle top slag composition before vacuum treatment (FeO wt%)+(MnO wt%)=6.7%, [(CaO wt%)+(MgO wt%)] / (Al 2 o 3 wt%)=1.72, and the slag thickness is 130mm.
[0031] In the RH furnace, vacuum decarburization treatment is carried out so that the carbon in the molten steel is below the required value of the finished product. After the vacuum decarburization is completed, Al is added to deoxidize the molten steel, followed by adding a refining agent of 0.7kg / t steel from the high-level silo. The composition of the refining agent is shown in Table 1. The molten steel is purely circulated for 2-7 minutes, the molten steel is alloyed, and the composition of the molten steel is adjusted to the specification range. The molten steel is purel...
Embodiment 2
[0034] Converter blowing is completed, [C] = 340ppm, [O] = 580ppm, slag blocking and tapping, to ensure that the ladle slag thickness is ≤ 50mm, add lime 2.3-2.7kg / t steel at the beginning of tapping, and add aluminum slag 0.9-1.2kg at the end / t steel, ladle top slag composition (FeOwt%)+(MnOwt%)=6.5% before vacuum treatment, [(CaO wt%)+(MgOwt%)] / (Al 2 o 3 wt%)=1.77, and the slag thickness is 132mm.
[0035] In the RH furnace, vacuum decarburization treatment is carried out so that the carbon in the molten steel is below the required value of the finished product. After the vacuum decarburization is completed, Al is added to deoxidize the molten steel, followed by adding a refining agent of 1.04kg / t steel from the high-level silo. The composition of the refining agent is shown in Table 1. The molten steel is purely circulated for 2-8 minutes, the molten steel is alloyed, and the composition of the molten steel is adjusted to the specification range. The molten steel purely...
Embodiment 3
[0038] Converter blowing is completed, [C] = 270ppm, [O] = 645ppm, slag is blocked and tapped to ensure ladle slag thickness ≤ 50mm, lime 2.5-3.4kg / t steel is added at the beginning of tapping, and aluminum slag is added at the end 0.7-0.9kg / t steel, ladle top slag composition (FeOwt%)+(MnOwt%)=6.2% before vacuum treatment, [(CaO wt%)+(MgOwt%)] / (Al 2 o 3 wt%)=1.82, and the slag thickness is 133mm.
[0039] In the RH furnace, vacuum decarburization treatment is carried out so that the carbon in the molten steel is below the required value of the finished product. After the vacuum decarburization is completed, Al is added to deoxidize the molten steel, followed by adding a refining agent of 0.48kg / t steel from the high-level silo. The composition of the refining agent is shown in Table 1. The molten steel is purely circulated for 3-7 minutes, the molten steel is alloyed, and the composition of the molten steel is adjusted to the specification range. The molten steel is purel...
PUM
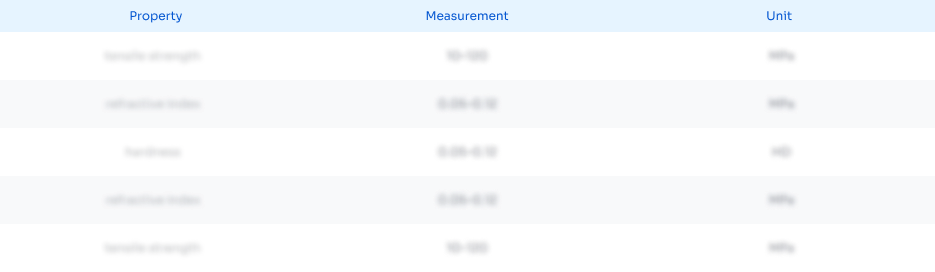
Abstract
Description
Claims
Application Information

- R&D
- Intellectual Property
- Life Sciences
- Materials
- Tech Scout
- Unparalleled Data Quality
- Higher Quality Content
- 60% Fewer Hallucinations
Browse by: Latest US Patents, China's latest patents, Technical Efficacy Thesaurus, Application Domain, Technology Topic, Popular Technical Reports.
© 2025 PatSnap. All rights reserved.Legal|Privacy policy|Modern Slavery Act Transparency Statement|Sitemap|About US| Contact US: help@patsnap.com