HC six-roller mill middle roller body end chamfer grinding method
A six-high rolling mill and intermediate roll technology, which is applied in the field of chamfering and grinding the end of the intermediate roll of the HC six-high rolling mill, can solve problems such as peeling of the end of the intermediate roll body, economic impact on safety, and scrapping of the intermediate roll. Achieve the effects of reducing abnormal loss, solving end ring cracks and peeling, and avoiding stress concentration
- Summary
- Abstract
- Description
- Claims
- Application Information
AI Technical Summary
Problems solved by technology
Method used
Image
Examples
Embodiment 1)
[0014] The chamfering grinding method of the end of the middle roll body of the HC six-high rolling mill of the present embodiment is as follows:
[0015] ① The chamfering structure design of the end of the roller body.
[0016] see figure 1 , In this embodiment, the chamfering structure of the middle roll body of the HC six-high rolling mill is designed to be R4000mm×100mm, and the unilateral drop is 1.25mm.
[0017] ②Chamfer grinding process at the end of the roller body.
[0018] Grinding is performed directly on the HERKULES CNC grinding machine. In the grinding parameter input column, input the grinding radius R4000mm, and set the width to 100mm. In this way, a grinding curve is output, and the built-in system grinds according to this curve.
[0019] According to the normal grinding feed amount and retraction amount of the roll body, each pass of grinding is carried out, and the chamfering angle difference at the end of the roll body is finally controlled to 1.25mm.
...
Embodiment 2)
[0024] The chamfering grinding method of the end of the middle roll body of the HC six-high rolling mill of the present embodiment is as follows:
[0025] ① The chamfering structure design of the end of the roller body.
[0026] see figure 2 In this embodiment, the chamfering structure at the end of the middle roll body of the HC six-high rolling mill is designed to be 35°×50mm+R1000mm×50mm.
[0027] ②Chamfer grinding process at the end of the roller body.
[0028] First, the end of the roll body is turned into a chamfer structure of 35°×50mm, and then it is ground on a HERKULES CNC grinding machine, and the grinding radius R1000mm is input in the grinding parameter input column, and the width is set to 50mm, so that a grinding line is output Grinding curve, the self-contained system will grind according to the curve.
[0029] The specific grinding parameters are also shown in Table 1.
PUM
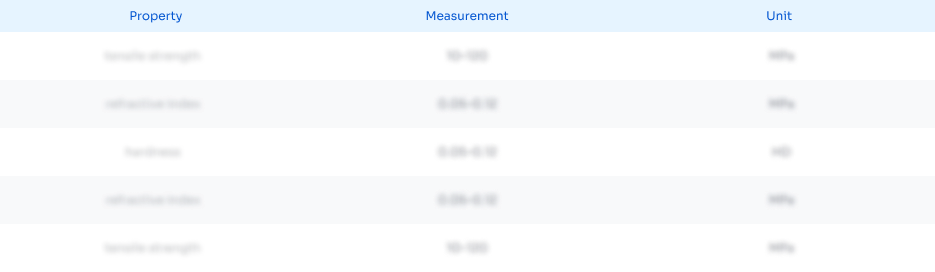
Abstract
Description
Claims
Application Information

- Generate Ideas
- Intellectual Property
- Life Sciences
- Materials
- Tech Scout
- Unparalleled Data Quality
- Higher Quality Content
- 60% Fewer Hallucinations
Browse by: Latest US Patents, China's latest patents, Technical Efficacy Thesaurus, Application Domain, Technology Topic, Popular Technical Reports.
© 2025 PatSnap. All rights reserved.Legal|Privacy policy|Modern Slavery Act Transparency Statement|Sitemap|About US| Contact US: help@patsnap.com