Method of preparing target material for high-purity aero-engine blade bonding coating
A technology of aero-engine and bonding coating, which is applied in coating, vacuum evaporation plating, metal material coating process, etc., and can solve the problems of unfavorable target performance, improvement, and low target purity.
- Summary
- Abstract
- Description
- Claims
- Application Information
AI Technical Summary
Problems solved by technology
Method used
Examples
Embodiment 1
[0029] Example 1: A method for preparing a high-purity aero-engine blade bond coating target
[0030] Include the following steps in order:
[0031] 1) Raw material pretreatment: After polishing the surface scale of Ni block, Co block, Cr block, Al block and Y block, use acetone to clean ultrasonically at a frequency of 20-30KHz twice, each time for 5 min, and clean Finally, put it in an oven and dry it at 373K for 10-30 minutes to obtain the pretreated target raw material;
[0032]2) Crucible and ingot mold pretreatment: Put the vacuum induction smelted graphite ingot mold and the graphite ingot mold molded in the molding sand box into the resistance furnace when the temperature is raised to 1173K, and keep it warm for 2 to 4 hours;
[0033] 3) Crucible and ingot mold installation: install the crucible and the fully preheated ingot mold in the vacuum induction melting furnace, clean the crucible and ingot mold, and install a ceramic filter on the sprue cup;
[0034] 4) Batc...
Embodiment 2
[0045] Example 2: A method for preparing a high-purity aeroengine blade bond coating target
[0046] Include the following steps in order:
[0047] 1) Raw material pretreatment: After polishing the surface scale of Ni block, Co block, Cr block, Al block and Y block, use acetone to clean ultrasonically at a frequency of 20-30KHz twice, each time for 5 min, and clean Finally, put it in an oven and dry it at 373K for 10-30 minutes to obtain the pretreated target raw material;
[0048] 2) Crucible and ingot mold pretreatment: Put the vacuum induction smelted graphite ingot mold and the graphite ingot mold molded in the molding sand box into the resistance furnace when the temperature is raised to 1173K, and keep it warm for 2 to 4 hours;
[0049] 3) Crucible and ingot mold installation: install the crucible and the fully preheated ingot mold in the vacuum induction melting furnace, clean the crucible and ingot mold, and install a ceramic filter on the sprue cup;
[0050] 4) Batc...
Embodiment 3
[0061] Example 3: A method for preparing a high-purity aeroengine blade bond coating target
[0062] Include the following steps in order:
[0063] 1) Raw material pretreatment: After polishing the surface scale of Ni block, Co block, Cr block, Al block and Y block, use acetone to clean ultrasonically at a frequency of 20-30KHz twice, each time for 5 min, and clean Finally, put it in an oven and dry it at 373K for 10-30 minutes to obtain the pretreated target raw material;
[0064] 2) Crucible and ingot mold pretreatment: Put the vacuum induction smelted graphite ingot mold and the graphite ingot mold molded in the molding sand box into the resistance furnace when the temperature is raised to 1173K, and keep it warm for 2 to 4 hours;
[0065] 3) Crucible and ingot mold installation: install the crucible and the fully preheated ingot mold in the vacuum induction melting furnace, clean the crucible and ingot mold, and install a ceramic filter on the sprue cup;
[0066] 4) Batc...
PUM
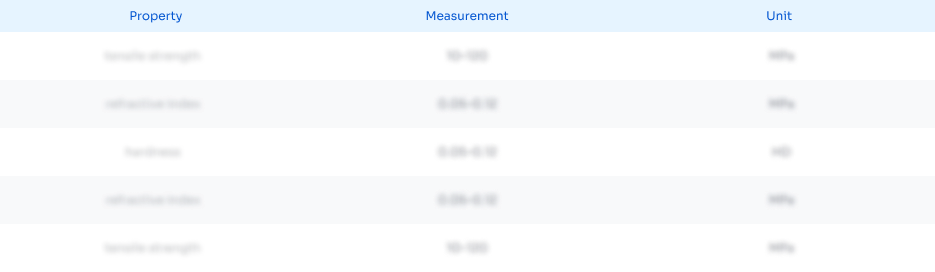
Abstract
Description
Claims
Application Information

- R&D
- Intellectual Property
- Life Sciences
- Materials
- Tech Scout
- Unparalleled Data Quality
- Higher Quality Content
- 60% Fewer Hallucinations
Browse by: Latest US Patents, China's latest patents, Technical Efficacy Thesaurus, Application Domain, Technology Topic, Popular Technical Reports.
© 2025 PatSnap. All rights reserved.Legal|Privacy policy|Modern Slavery Act Transparency Statement|Sitemap|About US| Contact US: help@patsnap.com