A method of processing plant material
A technology for plant raw materials and raw materials, applied in the field of processing plant raw materials, can solve problems such as full utilization of unfavorable energy, low product conversion rate, etc., and achieve the effects of excellent performance, low corrosiveness, and reduction of reaction temperature and energy consumption.
- Summary
- Abstract
- Description
- Claims
- Application Information
AI Technical Summary
Problems solved by technology
Method used
Image
Examples
Embodiment 1
[0059] (1) Pulverize the eucalyptus wood, extract it with hot water at 60°C for 3 hours, and then sieve it through a 200-mesh sieve to remove impurities to obtain pretreated raw materials;
[0060] (2) Add the pretreated raw material and butanol aqueous solution to the reaction vessel at a material-to-liquid ratio of 1:10, then add 2% oxalic acid, 2% acetic acid, and 1% hydrogen peroxide, wherein butanol in the butanol aqueous solution The mass concentration is 95%, and after mixing, heat at 180°C for 4 hours to obtain the reaction product;
[0061] (3) Separating the reaction product into solid-liquid to obtain fiber I and treatment liquid, using 60°C butanol to wash fiber I, the ratio of solid to liquid is 1:10, and the number of times is 5 times, and separating washing liquid and fiber II, using 60 Washing fiber II at ℃ to obtain slurry and washing liquid, the ratio of solid to liquid is 1:10, the number of times is 5 times, and the slurry is dried to obtain raw pulp fiber;...
Embodiment 2
[0065] (1) Grinding the eucalyptus wood, extracting with hot water at 30°C for 5 hours, and then sieving through a 100-mesh sieve to remove impurities to obtain pretreated raw materials;
[0066] (2) Add the pretreated raw material and butanol aqueous solution to the reaction vessel at a material-to-liquid ratio of 1:1, then add 0.1% potassium sulfate and 3% oxygen, wherein the mass concentration of butanol in the butanol aqueous solution is 90% , mixed and heated at 140°C for 3 hours to obtain the reaction product;
[0067] (3) Separating the reaction product into solid-liquid to obtain fiber I and treatment liquid, using butanol at 30°C to wash fiber I, the ratio of solid to liquid is 1:1, and the number of times is 10 times, to separate washing liquid and fiber II, and continue to use Wash the fiber II at 30°C to obtain slurry and washing liquid, the ratio of solid to liquid is 1:7, the number of times is 3 times, and the slurry is dried to obtain the original pulp fiber; ...
Embodiment 3
[0071] (1) Grinding corn stalks, extracting with hot water at 100°C for 1 hour, and then sieving with 400 meshes to remove impurities to obtain pretreated raw materials;
[0072] (2) Add the pretreated raw material and butanol aqueous solution to the reaction vessel according to the ratio of material to liquid at 1:25, then add 3% hydrochloric acid, 2% potassium dihydrogen phosphate, 2% calcium citrate, and 1% lemon Potassium acid potassium and 0.1% oxygen, wherein the mass concentration of butanol in the butanol aqueous solution is 50%, after mixing, heat at 130° C. for 6 hours to obtain the reaction product;
[0073] (3) Separating the reaction product into solid and liquid to obtain fiber I and treatment liquid, using 80°C butanol to wash fiber I, the ratio of solid to liquid is 1:20, and the number of times is 1, separate the washing liquid and fiber II, and continue to use 80°C Washing fiber II at ℃ to obtain slurry and washing liquid, the ratio of solid to liquid is 1:16...
PUM
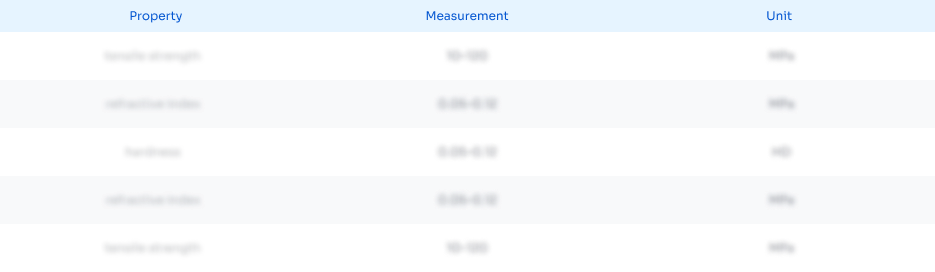
Abstract
Description
Claims
Application Information

- Generate Ideas
- Intellectual Property
- Life Sciences
- Materials
- Tech Scout
- Unparalleled Data Quality
- Higher Quality Content
- 60% Fewer Hallucinations
Browse by: Latest US Patents, China's latest patents, Technical Efficacy Thesaurus, Application Domain, Technology Topic, Popular Technical Reports.
© 2025 PatSnap. All rights reserved.Legal|Privacy policy|Modern Slavery Act Transparency Statement|Sitemap|About US| Contact US: help@patsnap.com