A kind of processing surface quality control method
A surface and quality processing technology, which is applied in the direction of metal processing equipment, metal processing machinery parts, manufacturing tools, etc., can solve problems such as failure to roll normally, lack of feedback function of rolling force, and increased force on the workpiece, so as to improve the quality of the workpiece. Processing efficiency and processing quality, saving special rolling equipment, enhanced rolling effect
- Summary
- Abstract
- Description
- Claims
- Application Information
AI Technical Summary
Problems solved by technology
Method used
Image
Examples
Embodiment Construction
[0041] The following will clearly and completely describe the technical solutions in the embodiments of the present invention with reference to the accompanying drawings in the embodiments of the present invention. Obviously, the described embodiments are only some, not all, embodiments of the present invention. Based on the embodiments of the present invention, all other embodiments obtained by persons of ordinary skill in the art without making creative efforts belong to the protection scope of the present invention.
[0042] 1. Set up the turning-ball rolling combined type processing device that characterizes the method of the present invention:
[0043] Such as Figure 1-3 As shown, the turning-ball tumbling combined processing device consists of a tumbling component 1, a bracket component 2, a base component 3, a workpiece 4, a sleeve 101, a tumbling body shell 102, a force-measuring bolt 103, and a gasket 104 , spring 105, dowel bar 106, support ring 107, rolling ball 1...
PUM
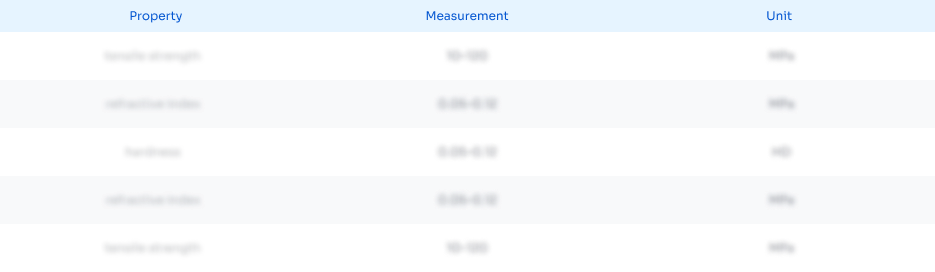
Abstract
Description
Claims
Application Information

- R&D
- Intellectual Property
- Life Sciences
- Materials
- Tech Scout
- Unparalleled Data Quality
- Higher Quality Content
- 60% Fewer Hallucinations
Browse by: Latest US Patents, China's latest patents, Technical Efficacy Thesaurus, Application Domain, Technology Topic, Popular Technical Reports.
© 2025 PatSnap. All rights reserved.Legal|Privacy policy|Modern Slavery Act Transparency Statement|Sitemap|About US| Contact US: help@patsnap.com