Piezoelectric MEMS microphone
A microphone and piezoelectric technology, applied in the field of piezoelectric MEMS microphones, can solve problems such as uneven stress distribution, uneven deformation, affecting microphone sensitivity and anti-drop performance, so as to improve uniformity, reduce structural differences, Effect of improving drop resistance
- Summary
- Abstract
- Description
- Claims
- Application Information
AI Technical Summary
Problems solved by technology
Method used
Image
Examples
Embodiment 1
[0025] Please refer to image 3 and Figure 4 , the present invention provides a piezoelectric MEMS microphone 100, which includes a substrate 1 with a back cavity 10, a piezoelectric diaphragm 2 disposed on the substrate 1, and a constraint located in the central region of the piezoelectric diaphragm 2 Structure 3. The base 1 is made of semiconductor material, such as silicon, and the back cavity 10 runs through the base 1 longitudinally, wherein the back cavity 10 can be formed by bulk silicon process or dry etching. The cross-sectional area of the back cavity 10 is smaller than that of the piezoelectric diaphragm 2 , and the cross-sectional area of the constraint structure 3 is smaller than that of the back cavity 10 .
[0026] The piezoelectric vibrating film 2 is generally circular, and its periphery is fixed to the base 1 , and other parts are suspended above the back cavity 10 of the base 1 . The piezoelectric diaphragm 2 includes a plurality of diaphragms 21 . ...
Embodiment 2
[0032] see Figure 5 , the piezoelectric MEMS microphone 200 provided in this embodiment is substantially the same as the piezoelectric MEMS microphone 100 in Embodiment 1, the main difference is that a plurality of the diaphragms 21 cooperate with the constraining structure 3 to form a square structure . The piezoelectric diaphragm 2 includes four diaphragms 21 , and the constraining structure 3 located in the central area of the piezoelectric diaphragm 2 is a square mesh structure. The other structures are substantially the same and will not be repeated here.
[0033] Compared with the related art, the piezoelectric MEMS microphone of the present invention restricts the free end 212 of the diaphragm 21 in the same plane by setting the constraint structure 3, when the diaphragm 21 is released from the base 1, the The constraint structure 3 can limit the degree of deformation of the diaphragm 21, so that the gap between two adjacent diaphragms 21 is consistent, reducing the...
PUM
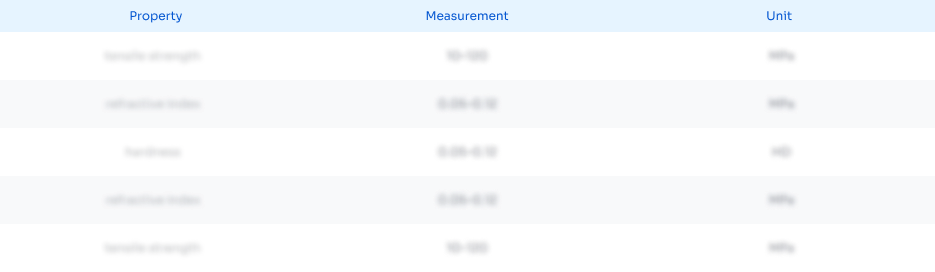
Abstract
Description
Claims
Application Information

- R&D Engineer
- R&D Manager
- IP Professional
- Industry Leading Data Capabilities
- Powerful AI technology
- Patent DNA Extraction
Browse by: Latest US Patents, China's latest patents, Technical Efficacy Thesaurus, Application Domain, Technology Topic, Popular Technical Reports.
© 2024 PatSnap. All rights reserved.Legal|Privacy policy|Modern Slavery Act Transparency Statement|Sitemap|About US| Contact US: help@patsnap.com